Acoplamento para Redutor é Essencial para o Desempenho Mecânico
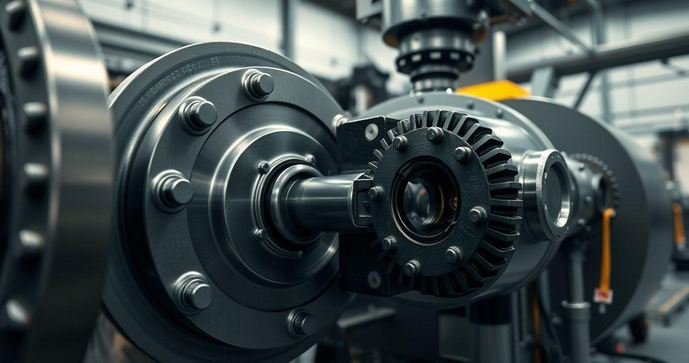
Por: Rodrigo - 16 de Abril de 2025
Entendendo o que é um Acoplamento para Redutor
O acoplamento para redutor é um componente mecânico fundamental que conecta dois eixos, permitindo a transmissão de torque e potência de um motor para um redutor. Sua principal função é estabelecer uma ligação entre o eixo do motor e o eixo do redutor, garantindo que ambos operem em harmonia.
Existem diferentes tipos de acoplamentos, cada um projetado para atender a requisitos específicos de desempenho. Alguns modelos são flexíveis, permitindo pequenas variações no alinhamento dos eixos, enquanto outros são rígidos, oferecendo uma conexão mais firme. Essa variação é importante para reduzir o desgaste dos componentes e aumentar a eficiência do sistema.
A escolha correta do acoplamento é vital, pois ele deve suportar as cargas e condições de operação do sistema, incluindo vibrações e movimentos radiais. Um acoplamento mal selecionado pode levar ao desgaste prematuro dos componentes, ruídos excessivos e falhas no sistema mecânico.
Além de facilitar a transmissão de potência, o acoplamento para redutor também desempenha um papel crucial na proteção do motor e do redutor contra sobrecargas. Em caso de um evento de sobrecarga, o acoplamento pode desgastar-se ou se romper, evitando que os componentes internos quebrem.
Em resumo, entender o funcionamento e a importância do acoplamento para redutor é essencial para projetos de engenharia mecânica. Ele não apenas assegura que o sistema opere eficientemente, mas também contribui para a longevidade dos equipamentos envolvidos.
Tipos de Acoplamentos para Redutores e suas Aplicações
Existem diversos tipos de acoplamentos para redutores, cada um projetado para atender a diferentes necessidades de aplicação. Abaixo, apresentamos os principais tipos e suas respectivas aplicações.
1. Acoplamentos Rígidos: Os acoplamentos rígidos conectam dois eixos de forma direta, sem permitir movimentação. Eles são ideais para sistemas onde o alinhamento é perfeito e a transmissão de torque precisa ser precisa e eficiente. Este tipo é comumente utilizado em máquinas que operam sob condições estáveis.
2. Acoplamentos Flexíveis: Ao contrário dos rígidos, os acoplamentos flexíveis permitem um certo grau de movimento entre os eixos, o que ajuda a compensar desalinhamentos e vibrações. Eles são frequentemente utilizados em sistemas que enfrentam variações dinâmicas, como em motores elétricos.
3. Acoplamentos de Borracha: Esses acoplamentos possuem elementos de borracha que oferecem amortecimento de vibrações e são usados em aplicações onde é importante minimizar o choque e o desgaste. Eles são comuns em veículos e maquinários pesados.
4. Acoplamentos de Engrenagem: Este tipo utiliza engrenagens para realizar a conexão, proporcionando alta precisão e eficiência. Os acoplamentos de engrenagem são ideais em aplicações de alta carga e foram projetados para suportar torques elevados.
5. Acoplamentos Híbridos: Combinando características de acoplamentos rígidos e flexíveis, os acoplamentos híbridos oferecem versatilidade e adaptabilidade a diversas situações. São usados em projetos variados, desde aplicações industriais até sistemas automotivos.
6. Acoplamentos por Mola: Utilizando molas para acomodar variações de movimento, esses acoplamentos são capazes de suportar altas taxas de rotação e são usados em aplicações onde a flexibilidade é crítica.
Cada tipo de acoplamento tem suas características únicas, tornando-os mais adequados para determinadas aplicações. A escolha do acoplamento correto é fundamental para garantir a eficiência e a durabilidade do sistema de transmissão de potência.
Benefícios de Utilizar Acoplamentos de Qualidade
A escolha de acoplamentos de qualidade é crucial para o desempenho e a durabilidade de sistemas mecânicos. Estes componentes não apenas desempenham uma função funcional, mas também oferecem uma série de benefícios tangíveis.
1. Aumento da Eficiência: Acoplamentos de alta qualidade garantem uma melhor transmissão de torque, reduzindo as perdas de energia durante a operação. Isso resulta em um sistema mais eficiente, que pode levar a uma economia significativa de energia nos processos industriais.
2. Menor Manutenção: Acoplamentos com materiais de alta qualidade e engenharia avançada exigem manutenção menos frequente. Isso se traduz em menos paradas inesperadas e custos reduzidos com reparos e substituições, tornando o sistema mais confiável.
3. Durabilidade Prolongada: Com materiais resistentes a desgaste, corrosão e altas temperaturas, os acoplamentos de qualidade são projetados para durar mais. Isso impacta diretamente a vida útil dos equipamentos, evitando falhas precoces.
4. Aprimoramento da Segurança: Acoplamentos de qualidade têm formas de prevenção contra falhas e sobrecargas, o que ajuda a proteger não apenas os motores e redutores, mas também os operadores e funcionários nas instalações. Um sistema bem projetado minimiza o risco de acidentes.
5. Redução de Ruídos e Vibrações: Acoplamentos de boa qualidade, especialmente os flexíveis, são eficazes em amortecer vibrações e reduzir ruídos durante a operação. Isso melhora o ambiente de trabalho e contribui para a longevidade do equipamento.
6. Versatilidade em Aplicações: Acoplamentos de alta qualidade são projetados para se adequar a diversas aplicações e condições de operação. Eles são adaptáveis e podem ser utilizados em diferentes máquinas e setores, oferecendo soluções eficientes para vários desafios.
Em suma, utilizar acoplamentos de qualidade não é apenas uma questão de eficiência mecânica; trata-se também de segurança, economia e desempenho geral do sistema. A escolha acertada pode resultar em operações mais suaves e econômicas, além de garantir maior durabilidade dos equipamentos.
Os Principais Fatores a Considerar na Escolha do Acoplamento
A escolha do acoplamento adequado é um passo crucial para garantir a eficiência e a segurança de qualquer sistema de transmissão de potência. Vários fatores devem ser considerados durante este processo, assegurando que o acoplamento selecionado atenda às exigências da aplicação.
1. Alinhamento dos Eixos: O alinhamento correto dos eixos é fundamental na seleção do acoplamento. Se os eixos estiverem desalinhados, um acoplamento flexível pode ser necessário para compensar essa condição e evitar desgastes prematuros.
2. Tipo de Carga: Considerar a natureza da carga que será transmitida é essencial. Cargas variáveis, cargas de impacto e torques elevados devem ser levados em conta para escolher um acoplamento que suporte essas condições sem comprometer o sistema.
3. Frequência de Operação: O tempo e a frequência de uso do equipamento influenciam a escolha do acoplamento. Para aplicações contínuas, um acoplamento de alta durabilidade e resistência ao desgaste é ideal, enquanto para uso intermitente, opções mais flexíveis podem ser consideradas.
4. Condições Ambientais: As condições em que o acoplamento será utilizado, como temperatura, umidade, poeira e produtos químicos, também impactam a seleção. Acoplamentos fabricados com materiais resistentes a corrosão e desgastes são preferíveis em ambientes agressivos.
5. Manutenção Necessária: A simplicidade na manutenção deve ser considerada. Acoplamentos que exigem manutenção frequente podem aumentar os custos operacionais e o tempo de inatividade, enquanto os modelos que oferecem maior durabilidade e menos requisitos de manutenção são mais vantajosos.
6. Compatibilidade com Componentes: A compatibilidade entre o acoplamento, motor e redutor é crucial. Certifique-se de que as dimensões, características técnicas e requisitos de potência dos componentes sejam compatíveis para evitar falhas de funcionamento.
Considerar esses fatores ao escolher o acoplamento certo para sua aplicação pode garantir um desempenho otimizado, durabilidade e segurança em todo o sistema de transmissão de potência. Uma seleção cuidadosa resultará em operações mais eficientes e prolongará a vida útil do equipamento.
Erros Comuns na Instalação de Acoplamentos para Redutores
A instalação adequada de acoplamentos para redutores é fundamental para o desempenho e a durabilidade do sistema. Contudo, diversos erros comuns podem ocorrer durante o processo de instalação, comprometendo a eficiência geral e a vida útil do equipamento.
1. Alinhamento Improprio: Um dos erros mais frequentes é o desalinhamento dos eixos durante a instalação. Isso pode resultar em desgaste excessivo, vibrações e até falhas mecânicas. Verificar o alinhamento com precisão é essencial para evitar esses problemas.
2. Falta de Lubrificação: Muitos instaladores esquecem de aplicar a lubrificação adequada nas partes móveis do acoplamento. A falta de lubrificação pode causar atrito excessivo, levando ao desgaste prematuro. É importante seguir as recomendações do fabricante sobre lubrificação.
3. Pressão Excessiva durante a Montagem: Aplicar força excessiva ao fixar o acoplamento pode causar deformações e danos nas peças. A montagem deve ser realizada com a pressão correta para garantir uma conexão segura sem comprometer a integridade do acoplamento.
4. Uso de Ferramentas Inadequadas: Utilizar ferramentas inadequadas pode resultar em danos ao acoplamento ou ao eixo. É vital empregar ferramentas apropriadas e seguir as diretrizes do fabricante para uma instalação correta e segura.
5. Não Conferir as Especificações Técnicas: Ignorar as especificações técnicas do acoplamento e dos eixos é um erro crítico. Cada acoplamento é projetado para operar dentro de determinados limites; não respeitar essas especificações pode ocasionar falhas.
6. Negligenciar o Teste Pós-Instalação: Após a instalação, muitos negligenciam a realização de testes para verificar o funcionamento adequado do sistema. Testes de funcionamento garantem que o acoplamento e os componentes estão interagindo corretamente e podem prevenir problemas futuros.
Evitar esses erros comuns na instalação de acoplamentos para redutores garantirá uma operação mais eficiente, reduzindo custos de manutenção e prolongando a vida útil dos equipamentos. Um planejamento cuidadoso e a atenção aos detalhes são essenciais para o sucesso da instalação.
Manutenção Necessária para Prolongar a Vida Útil do Acoplamento
A manutenção regular é essencial para garantir a eficiência e prolongar a vida útil dos acoplamentos utilizados em redutores. Seguir um plano de manutenção adequado não apenas evita falhas, mas também assegura que o sistema funcione de forma ideal.
1. Inspeção Visual Regular: Realizar inspeções visuais frequentes é fundamental para identificar sinais de desgaste, folgas ou danos. Observações minuciosas podem ajudar na detecção precoce de problemas, permitindo ações corretivas antes que se tornem mais sérios.
2. Lubrificação Adequada: A lubrificação é vital para reduzir o atrito entre as peças móveis do acoplamento. Verifique e aplique lubrificante conforme as especificações do fabricante. A manutenção regular da lubrificação aumenta a eficiência e a durabilidade do acoplamento.
3. Verificação de Alinhamento: O alinhamento dos eixos deve ser verificado periodicamente, especialmente após os ajustes ou substituições do acoplamento. Manter o alinhamento correto minimiza o desgaste e as vibrações, contribuindo para um funcionamento mais suave.
4. Testes de Desempenho: Realizar testes de desempenho após a instalação e em intervalos regulares ajudará a monitorar o funcionamento do acoplamento. Isso inclui verificar a eficiência na transmissão de torque e observar sinais de vibrações incomuns.
5. Troca de Peças Desgastadas: Componentes que apresentarem sinais de desgaste devem ser substituídos imediatamente. Isso pode incluir o próprio acoplamento, se necessário. A troca tempestiva de peças evita falhas e aumenta a confiabilidade do sistema.
6. Documentação: Manter um registro detalhado de todas as manutenções realizadas, incluindo inspeções, lubrificações e substituições de peças, é vital. Isso não apenas ajuda a acompanhar a condição do equipamento, mas também serve como referência para futuros processos de manutenção.
Seguir estas práticas de manutenção garantirá que o acoplamento continue a operar eficientemente e prolongará sua vida útil. Um sistema bem mantido não apenas melhora a produtividade, mas também reduz custos com reparos e substituições.
A escolha e instalação adequadas de acoplamentos para redutores são cruciais para garantir o desempenho e a durabilidade dos sistemas de transmissão. Considerar fatores como alinhamento, tipo de carga e condições ambientais é fundamental para uma seleção eficaz.
Além disso, a manutenção regular, incluindo inspeções visuais, lubrificação e testes de desempenho, assegura que os acoplamentos funcionem de maneira ideal e prolonga sua vida útil. Evitar erros comuns durante a instalação e adotar boas práticas de manutenção pode prevenir falhas e economizar recursos.
Em resumo, investir tempo na escolha, instalação e manutenção de acoplamentos de qualidade resulta em operações mais eficientes e confiáveis. Esse investimento não apenas aprimora o desempenho mecânico, mas também contribui para a segurança e sustentabilidade dos equipamentos.