Acoplamento para Redutor: Como Escolher o Ideal para Sua Aplicação
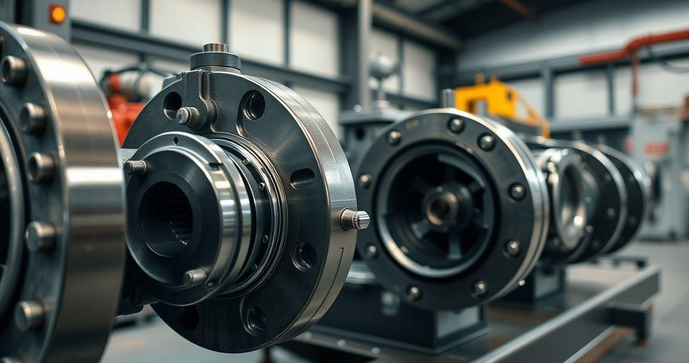
Por: Rodrigo - 24 de Janeiro de 2025
O acoplamento para redutor desempenha um papel crucial na transmissão de torque e na eficiência de sistemas mecânicos. Com a variedade de opções disponíveis no mercado, escolher o acoplamento adequado pode ser um desafio. Neste artigo, abordaremos os diferentes tipos de acoplamentos, suas aplicações, e forneceremos dicas valiosas para garantir que você faça a melhor escolha para suas necessidades específicas.
1. Tipos de Acoplamentos para Redutores e Suas Aplicações
Os acoplamentos para redutores são componentes essenciais em sistemas mecânicos, pois permitem a conexão entre eixos, transmitindo torque e movimento de forma eficiente. Existem diversos tipos de acoplamentos, cada um com características específicas que os tornam mais adequados para determinadas aplicações. A seguir, exploraremos os principais tipos de acoplamentos para redutores e suas respectivas aplicações.
1. Acoplamentos Rígidos
Os acoplamentos rígidos são utilizados para conectar eixos que estão alinhados de forma precisa. Eles não permitem qualquer movimento angular ou axial entre os eixos, o que os torna ideais para aplicações onde a precisão é fundamental. Esses acoplamentos são frequentemente encontrados em máquinas que exigem alta precisão, como em sistemas de transmissão de potência em indústrias de manufatura.
2. Acoplamentos Flexíveis
Os acoplamentos flexíveis são projetados para acomodar desalinhamentos entre os eixos, permitindo uma certa flexibilidade. Eles são essenciais em aplicações onde o alinhamento perfeito não é garantido, como em sistemas que sofrem variações térmicas ou vibrações. Esses acoplamentos podem ser feitos de materiais como borracha ou poliuretano, que absorvem choques e reduzem o desgaste. São comumente utilizados em motores elétricos e redutores em indústrias de mineração e construção.
3. Acoplamentos de Deslizamento
Os acoplamentos de deslizamento são projetados para permitir um movimento axial entre os eixos. Eles são frequentemente utilizados em aplicações onde é necessário compensar o alongamento térmico ou a movimentação dos eixos. Esses acoplamentos são comuns em sistemas de transmissão de potência em equipamentos pesados, como guindastes e escavadeiras, onde o movimento axial pode ocorrer devido ao peso e à carga aplicada.
4. Acoplamentos de Engrenagem
Os acoplamentos de engrenagem são utilizados para transmitir torque entre eixos que podem estar desalinhados. Eles são projetados com dentes que se encaixam, permitindo uma transmissão de potência eficiente. Esses acoplamentos são ideais para aplicações que exigem alta resistência e durabilidade, como em redutores de velocidade em indústrias de papel e celulose. A capacidade de suportar altas cargas e a resistência ao desgaste tornam os acoplamentos de engrenagem uma escolha popular em ambientes industriais exigentes.
5. Acoplamentos de Membrana
Os acoplamentos de membrana são projetados para transmitir torque enquanto permitem um certo grau de flexibilidade. Eles são compostos por uma ou mais membranas que se deformam para acomodar desalinhamentos. Esses acoplamentos são frequentemente utilizados em aplicações de alta velocidade, como em turbinas e compressores, onde a precisão e a capacidade de absorver vibrações são cruciais. A leveza e a eficiência dos acoplamentos de membrana os tornam uma escolha popular em indústrias de energia e automação.
6. Acoplamentos Bipartidos
Os acoplamentos bipartidos são uma solução prática para a conexão de eixos, permitindo fácil instalação e manutenção. Eles são compostos por duas partes que se conectam no meio, facilitando a montagem e a desmontagem. Este tipo de acoplamento é ideal para aplicações onde o espaço é limitado ou onde a manutenção frequente é necessária. O Acoplamento bipartido é amplamente utilizado em sistemas de transmissão de potência em máquinas agrícolas e equipamentos de construção, onde a facilidade de acesso é um fator importante.
7. Acoplamentos Hidráulicos
Os acoplamentos hidráulicos utilizam fluido para transmitir torque entre os eixos. Eles são projetados para permitir uma certa quantidade de deslizamento, o que ajuda a proteger os componentes do sistema contra sobrecargas. Esses acoplamentos são frequentemente utilizados em aplicações que exigem uma transmissão suave de potência, como em sistemas de transmissão de veículos e equipamentos pesados. A capacidade de absorver choques e vibrações torna os acoplamentos hidráulicos uma escolha ideal para ambientes industriais desafiadores.
Em resumo, a escolha do tipo de acoplamento para redutor depende das necessidades específicas da aplicação, incluindo alinhamento, flexibilidade e resistência. Compreender as características e aplicações de cada tipo de acoplamento é fundamental para garantir a eficiência e a durabilidade do sistema mecânico. Ao selecionar o acoplamento adequado, você pode otimizar o desempenho do seu redutor e prolongar a vida útil dos componentes envolvidos.
2. Como Escolher o Acoplamento Ideal para Seu Redutor
A escolha do acoplamento ideal para um redutor é uma etapa crucial no processo de engenharia e manutenção de sistemas mecânicos. Um acoplamento adequado não apenas garante a eficiência na transmissão de torque, mas também contribui para a durabilidade e a segurança do equipamento. Neste artigo, abordaremos os principais fatores a serem considerados ao selecionar o acoplamento ideal para seu redutor.
1. Alinhamento dos Eixos
Um dos primeiros aspectos a considerar é o alinhamento dos eixos que o acoplamento irá conectar. O alinhamento correto é fundamental para evitar desgastes prematuros e falhas no sistema. Se os eixos estiverem desalinhados, um acoplamento flexível pode ser a melhor escolha, pois ele pode acomodar pequenas variações de alinhamento. Por outro lado, se os eixos estiverem perfeitamente alinhados, um acoplamento rígido pode ser mais apropriado, pois oferece maior precisão na transmissão de torque.
2. Tipo de Carga
Outro fator importante é o tipo de carga que o redutor irá suportar. Cargas dinâmicas, como aquelas encontradas em sistemas que operam em altas velocidades ou que sofrem variações de carga, exigem acoplamentos que possam absorver choques e vibrações. Nesse caso, um acoplamento elástico de pinos pode ser uma excelente opção, pois ele proporciona uma absorção eficaz de impactos e reduz o desgaste dos componentes. Já em aplicações com cargas constantes, acoplamentos rígidos podem ser mais adequados.
3. Material do Acoplamento
O material do acoplamento também desempenha um papel significativo na escolha. Acoplamentos podem ser feitos de diversos materiais, como aço, alumínio, plástico e borracha. A escolha do material deve levar em consideração fatores como resistência à corrosão, temperatura de operação e ambiente de trabalho. Por exemplo, em ambientes agressivos, como indústrias químicas, acoplamentos de materiais resistentes à corrosão são essenciais para garantir a durabilidade do sistema.
4. Tamanho e Capacidade de Carga
O tamanho do acoplamento e sua capacidade de carga são aspectos fundamentais a serem considerados. É importante escolher um acoplamento que suporte o torque máximo que o redutor irá transmitir. Para isso, é necessário calcular o torque de operação e verificar as especificações do fabricante do acoplamento. Um acoplamento subdimensionado pode levar a falhas catastróficas, enquanto um acoplamento superdimensionado pode resultar em custos desnecessários.
5. Condições de Operação
As condições de operação, como temperatura, umidade e presença de contaminantes, também devem ser levadas em conta. Em ambientes com altas temperaturas, por exemplo, é fundamental escolher um acoplamento que mantenha suas propriedades mecânicas mesmo sob condições extremas. Além disso, se o ambiente for propenso a poeira ou umidade, acoplamentos com vedação adequada podem ser necessários para evitar a entrada de contaminantes que possam comprometer o funcionamento do sistema.
6. Facilidade de Instalação e Manutenção
A facilidade de instalação e manutenção do acoplamento é outro aspecto a ser considerado. Acoplamentos que permitem uma instalação rápida e fácil podem economizar tempo e custos durante a montagem do sistema. Além disso, a manutenção regular é essencial para garantir a longevidade do acoplamento. Portanto, escolha um modelo que permita acesso fácil para inspeções e manutenções periódicas.
7. Custo e Disponibilidade
Por fim, o custo e a disponibilidade do acoplamento também são fatores importantes. É essencial encontrar um equilíbrio entre qualidade e preço. Acoplamentos de alta qualidade podem ter um custo inicial mais elevado, mas podem resultar em economia a longo prazo devido à sua durabilidade e menor necessidade de manutenção. Além disso, verifique a disponibilidade do acoplamento no mercado, pois isso pode impactar o tempo de entrega e a implementação do sistema.
Em resumo, a escolha do acoplamento ideal para seu redutor envolve uma análise cuidadosa de diversos fatores, incluindo alinhamento dos eixos, tipo de carga, material, tamanho, condições de operação, facilidade de instalação e custo. Ao considerar todos esses aspectos, você poderá selecionar um acoplamento que não apenas atenda às suas necessidades, mas que também contribua para a eficiência e a durabilidade do seu sistema mecânico. A escolha correta do acoplamento é um investimento que pode resultar em maior produtividade e menor tempo de inatividade no seu equipamento.
3. Vantagens do Uso de Acoplamentos em Sistemas Mecânicos
Os acoplamentos desempenham um papel fundamental em sistemas mecânicos, conectando eixos e permitindo a transmissão eficiente de torque e movimento. A escolha de um acoplamento adequado pode trazer diversas vantagens para o funcionamento de máquinas e equipamentos. Neste artigo, discutiremos as principais vantagens do uso de acoplamentos em sistemas mecânicos.
1. Transmissão Eficiente de Torque
Uma das principais vantagens dos acoplamentos é a sua capacidade de transmitir torque de forma eficiente entre eixos. Eles garantem que a energia gerada por um motor seja transferida para o redutor ou outro componente do sistema, minimizando perdas de energia. Isso é especialmente importante em aplicações industriais, onde a eficiência energética é crucial para a redução de custos operacionais. Acoplamentos bem projetados, como o Acoplamento De Pino, são capazes de suportar altas cargas e garantir uma transmissão de torque suave e confiável.
2. Compensação de Desalinhamentos
Os acoplamentos também oferecem a vantagem de compensar desalinhamentos entre eixos. Em muitos sistemas mecânicos, é difícil garantir que os eixos estejam perfeitamente alinhados devido a variações térmicas, vibrações ou desgaste. Acoplamentos flexíveis são projetados para acomodar esses desalinhamentos, evitando tensões excessivas nos componentes e prolongando a vida útil do sistema. Essa capacidade de compensação é essencial para manter a eficiência e a confiabilidade do equipamento.
3. Absorção de Choques e Vibrações
Outra vantagem significativa dos acoplamentos é a sua capacidade de absorver choques e vibrações. Em sistemas que operam sob condições de carga variável, como em máquinas pesadas ou equipamentos de construção, os choques podem causar danos aos componentes. Acoplamentos flexíveis e elásticos são projetados para amortecer essas forças, protegendo o motor e outros componentes do sistema contra danos. Isso não apenas aumenta a durabilidade do equipamento, mas também melhora o conforto operacional.
4. Facilidade de Instalação e Manutenção
A instalação e manutenção de acoplamentos são geralmente simples e diretas. Muitos modelos são projetados para permitir uma instalação rápida, o que pode economizar tempo e custos durante a montagem do sistema. Além disso, a manutenção regular é facilitada pela acessibilidade dos acoplamentos, permitindo inspeções e ajustes sem a necessidade de desmontar todo o sistema. Essa facilidade de instalação e manutenção é uma vantagem importante em ambientes industriais, onde o tempo de inatividade deve ser minimizado.
5. Versatilidade de Aplicações
Os acoplamentos são extremamente versáteis e podem ser utilizados em uma ampla variedade de aplicações. Desde motores elétricos e redutores até bombas e compressores, os acoplamentos são componentes essenciais em muitos sistemas mecânicos. Essa versatilidade permite que os engenheiros escolham o tipo de acoplamento mais adequado para cada aplicação específica, garantindo que o sistema funcione de maneira otimizada. A diversidade de tipos de acoplamentos disponíveis no mercado também significa que há uma solução para praticamente qualquer necessidade de transmissão de potência.
6. Redução de Ruído
Os acoplamentos também podem contribuir para a redução do ruído em sistemas mecânicos. Em aplicações onde o ruído é uma preocupação, como em ambientes residenciais ou comerciais, acoplamentos que absorvem vibrações podem ajudar a minimizar o som gerado pelo funcionamento do equipamento. Isso é especialmente importante em indústrias que buscam atender a regulamentações de controle de ruído ou que desejam proporcionar um ambiente de trabalho mais confortável para os funcionários.
7. Aumento da Vida Útil dos Componentes
Ao proteger os componentes do sistema contra tensões excessivas, choques e vibrações, os acoplamentos contribuem para o aumento da vida útil dos equipamentos. Um acoplamento adequado pode reduzir o desgaste em motores, redutores e outros componentes, resultando em menos paradas para manutenção e substituição. Isso não apenas melhora a eficiência operacional, mas também reduz os custos associados à manutenção e ao reparo de equipamentos.
8. Melhoria na Segurança Operacional
Por fim, o uso de acoplamentos em sistemas mecânicos também pode melhorar a segurança operacional. Acoplamentos que absorvem choques e vibrações ajudam a evitar falhas catastróficas que podem resultar em acidentes. Além disso, a escolha de acoplamentos de alta qualidade e adequados para a aplicação específica pode reduzir o risco de falhas inesperadas, garantindo um ambiente de trabalho mais seguro para os operadores e funcionários.
Em resumo, os acoplamentos oferecem uma série de vantagens em sistemas mecânicos, incluindo transmissão eficiente de torque, compensação de desalinhamentos, absorção de choques e vibrações, facilidade de instalação e manutenção, versatilidade de aplicações, redução de ruído, aumento da vida útil dos componentes e melhoria na segurança operacional. Ao considerar essas vantagens, fica claro que a escolha do acoplamento adequado é fundamental para garantir a eficiência e a durabilidade dos sistemas mecânicos.
4. Instalação Correta de Acoplamentos para Redutores
A instalação correta de acoplamentos para redutores é uma etapa crucial para garantir o desempenho eficiente e a durabilidade do sistema mecânico. Um acoplamento mal instalado pode levar a problemas como desgaste prematuro, falhas mecânicas e até mesmo acidentes. Neste artigo, abordaremos as melhores práticas para a instalação de acoplamentos, destacando os passos essenciais e os cuidados a serem tomados durante o processo.
1. Preparação do Local de Trabalho
Antes de iniciar a instalação, é fundamental preparar o local de trabalho. Certifique-se de que a área esteja limpa e livre de obstruções. Remova qualquer sujeira, poeira ou detritos que possam interferir na instalação. Além disso, verifique se todas as ferramentas necessárias estão disponíveis e em boas condições. Ter um ambiente de trabalho organizado não apenas facilita a instalação, mas também contribui para a segurança do processo.
2. Verificação dos Componentes
Antes de instalar o acoplamento, é importante verificar todos os componentes envolvidos, incluindo os eixos, o redutor e o próprio acoplamento. Certifique-se de que os eixos estejam limpos e livres de ferrugem ou sujeira. Qualquer contaminação pode afetar a eficiência da conexão. Além disso, verifique se o acoplamento está em boas condições, sem rachaduras ou danos visíveis. Se necessário, consulte as especificações do fabricante para garantir que o acoplamento escolhido é adequado para a aplicação.
3. Alinhamento dos Eixos
Um dos aspectos mais críticos na instalação de acoplamentos é o alinhamento dos eixos. O alinhamento correto é essencial para evitar tensões excessivas e garantir uma transmissão eficiente de torque. Utilize ferramentas de alinhamento, como alinhadores a laser ou gabaritos de alinhamento, para verificar se os eixos estão alinhados de forma precisa. Se houver desalinhamento, ajuste a posição dos eixos antes de prosseguir com a instalação do acoplamento.
4. Montagem do Acoplamento
Após garantir que os eixos estão alinhados, é hora de montar o acoplamento. Siga as instruções do fabricante para a montagem correta. Em geral, isso envolve a colocação do acoplamento nas extremidades dos eixos e a fixação com parafusos ou outros dispositivos de fixação. Certifique-se de que o acoplamento esteja posicionado corretamente e que os parafusos estejam apertados de acordo com as especificações recomendadas. Um exemplo de acoplamento que pode ser utilizado é o Acoplamento omega, que é conhecido por sua facilidade de instalação e eficiência.
5. Verificação do Torque de Aperto
Após a montagem, é fundamental verificar o torque de aperto dos parafusos do acoplamento. O torque deve ser ajustado de acordo com as especificações do fabricante para garantir que o acoplamento esteja firmemente fixado. Um aperto inadequado pode levar a falhas no acoplamento, enquanto um aperto excessivo pode danificar os componentes. Utilize uma chave de torque para garantir que os parafusos estejam apertados corretamente.
6. Teste de Funcionamento
Após a instalação, é importante realizar um teste de funcionamento do sistema. Ligue o equipamento e observe o funcionamento do redutor e do acoplamento. Verifique se há vibrações excessivas, ruídos estranhos ou qualquer sinal de desalinhamento. Se notar algum problema, desligue o equipamento imediatamente e verifique a instalação. Realizar testes de funcionamento é essencial para garantir que o sistema esteja operando de forma eficiente e segura.
7. Manutenção Regular
A instalação correta é apenas o primeiro passo; a manutenção regular do acoplamento e do sistema mecânico é igualmente importante. Realize inspeções periódicas para verificar o estado do acoplamento, os eixos e o redutor. Procure sinais de desgaste, folgas ou danos. A manutenção preventiva pode ajudar a identificar problemas antes que se tornem críticos, prolongando a vida útil do equipamento e evitando paradas inesperadas.
8. Documentação e Registro
Por fim, é recomendável manter registros detalhados da instalação e da manutenção do acoplamento. Documentar as especificações do acoplamento, os procedimentos de instalação e as datas das manutenções pode ser útil para futuras referências. Além disso, essa documentação pode ser valiosa em caso de auditorias ou avaliações de segurança.
Em resumo, a instalação correta de acoplamentos para redutores envolve uma série de etapas, desde a preparação do local de trabalho até a verificação do funcionamento do sistema. Garantir o alinhamento adequado dos eixos, seguir as instruções do fabricante e realizar testes de funcionamento são práticas essenciais para garantir a eficiência e a durabilidade do sistema mecânico. Com a instalação adequada e a manutenção regular, você pode maximizar o desempenho do seu redutor e prolongar a vida útil dos componentes envolvidos.
5. Manutenção e Cuidados com Acoplamentos para Redutores
A manutenção adequada e os cuidados com acoplamentos para redutores são essenciais para garantir o desempenho eficiente e a durabilidade dos sistemas mecânicos. Acoplamentos desempenham um papel crucial na transmissão de torque e movimento, e sua integridade é fundamental para o funcionamento seguro e eficaz de máquinas e equipamentos. Neste artigo, abordaremos as melhores práticas de manutenção e cuidados que devem ser adotados para prolongar a vida útil dos acoplamentos.
1. Inspeções Regulares
Realizar inspeções regulares é uma das práticas mais importantes na manutenção de acoplamentos. As inspeções devem ser feitas com frequência, dependendo da intensidade de uso do equipamento e das condições operacionais. Durante as inspeções, verifique se há sinais de desgaste, folgas, rachaduras ou danos visíveis nos acoplamentos. Além disso, observe se há qualquer tipo de vibração excessiva ou ruído anormal durante a operação, pois esses podem ser indicativos de problemas que precisam ser abordados.
2. Limpeza dos Componentes
A limpeza dos acoplamentos e dos componentes adjacentes é fundamental para evitar a contaminação e o desgaste prematuro. Poeira, sujeira e detritos podem se acumular ao redor do acoplamento, interferindo em seu funcionamento. Utilize um pano limpo e seco para remover sujeira e detritos. Em ambientes industriais, onde a sujeira é mais comum, pode ser necessário realizar limpezas mais frequentes. Evite o uso de solventes agressivos que possam danificar os materiais do acoplamento.
3. Lubrificação Adequada
A lubrificação é um aspecto crítico na manutenção de acoplamentos, especialmente aqueles que possuem partes móveis. A falta de lubrificação pode levar ao aumento do atrito e ao desgaste prematuro dos componentes. Siga as recomendações do fabricante quanto ao tipo de lubrificante a ser utilizado e a frequência de aplicação. Em geral, a lubrificação deve ser realizada em intervalos regulares, conforme indicado nas especificações do acoplamento. Certifique-se de que a lubrificação seja feita de maneira adequada, evitando excessos que possam causar acúmulo de sujeira.
4. Verificação do Alinhamento
O alinhamento adequado dos eixos é fundamental para o funcionamento eficiente dos acoplamentos. Desalinhamentos podem causar tensões excessivas e desgaste prematuro. Realize verificações periódicas do alinhamento dos eixos e ajuste conforme necessário. Utilize ferramentas de alinhamento, como alinhadores a laser, para garantir que os eixos estejam alinhados corretamente. Se notar qualquer desalinhamento, faça os ajustes necessários imediatamente para evitar danos ao acoplamento e aos componentes adjacentes.
5. Monitoramento de Temperatura
A temperatura de operação dos acoplamentos deve ser monitorada regularmente. Temperaturas excessivas podem indicar problemas, como atrito excessivo ou falta de lubrificação. Utilize termômetros ou sensores de temperatura para monitorar a temperatura dos acoplamentos durante a operação. Se a temperatura exceder os limites recomendados pelo fabricante, desligue o equipamento e investigue a causa do problema. A correção de problemas de temperatura pode evitar falhas catastróficas e prolongar a vida útil do acoplamento.
6. Substituição de Componentes Danificados
Se durante as inspeções forem identificados componentes danificados ou desgastados, é fundamental realizar a substituição imediatamente. Ignorar componentes danificados pode levar a falhas mais sérias e a custos elevados de reparo. Consulte as especificações do fabricante para garantir que os componentes de reposição sejam compatíveis com o acoplamento existente. A substituição oportuna de componentes danificados é uma parte essencial da manutenção preventiva.
7. Registro de Manutenção
Manter um registro detalhado das atividades de manutenção é uma prática recomendada que pode ajudar a monitorar o desempenho dos acoplamentos ao longo do tempo. Registre as datas das inspeções, as atividades realizadas, as substituições de componentes e quaisquer problemas identificados. Esses registros podem ser úteis para identificar padrões de desgaste e para planejar futuras manutenções. Além disso, a documentação pode ser valiosa em caso de auditorias ou avaliações de segurança.
8. Treinamento da Equipe
Por fim, é importante garantir que a equipe responsável pela operação e manutenção dos equipamentos esteja devidamente treinada. O conhecimento sobre as melhores práticas de manutenção e cuidados com acoplamentos é fundamental para evitar erros que possam comprometer o desempenho do sistema. Realize treinamentos regulares e forneça informações atualizadas sobre os procedimentos de manutenção e as especificações dos acoplamentos utilizados.
Em resumo, a manutenção e os cuidados com acoplamentos para redutores são essenciais para garantir a eficiência e a durabilidade dos sistemas mecânicos. Inspeções regulares, limpeza, lubrificação adequada, verificação de alinhamento, monitoramento de temperatura, substituição de componentes danificados, registro de manutenção e treinamento da equipe são práticas fundamentais que devem ser adotadas. Ao seguir essas diretrizes, você pode maximizar o desempenho dos acoplamentos e prolongar a vida útil dos equipamentos, resultando em maior eficiência operacional e redução de custos com manutenção.
6. Erros Comuns ao Utilizar Acoplamentos em Redutores
O uso de acoplamentos em redutores é uma prática comum em sistemas mecânicos, mas existem erros que podem comprometer a eficiência e a durabilidade do equipamento. Compreender esses erros e como evitá-los é fundamental para garantir o funcionamento adequado do sistema. Neste artigo, abordaremos os erros mais comuns ao utilizar acoplamentos em redutores e como corrigi-los.
1. Desalinhamento dos Eixos
Um dos erros mais frequentes é o desalinhamento dos eixos. Quando os eixos não estão alinhados corretamente, isso pode causar tensões excessivas no acoplamento, levando a um desgaste prematuro e até mesmo a falhas catastróficas. Para evitar esse problema, é essencial realizar verificações de alinhamento regularmente, utilizando ferramentas apropriadas, como alinhadores a laser. Se o desalinhamento for identificado, ajustes devem ser feitos imediatamente para garantir que os eixos estejam alinhados corretamente.
2. Escolha Inadequada do Tipo de Acoplamento
Outro erro comum é a escolha inadequada do tipo de acoplamento para a aplicação específica. Cada tipo de acoplamento possui características distintas que o tornam mais adequado para determinadas situações. Por exemplo, acoplamentos rígidos são ideais para eixos perfeitamente alinhados, enquanto acoplamentos flexíveis são mais apropriados para situações onde há desalinhamento. Antes de selecionar um acoplamento, é importante considerar fatores como tipo de carga, alinhamento e condições de operação.
3. Falta de Lubrificação
A falta de lubrificação é um erro que pode levar a um aumento do atrito e ao desgaste prematuro dos componentes do acoplamento. Muitos acoplamentos possuem partes móveis que requerem lubrificação regular para funcionar de maneira eficiente. É fundamental seguir as recomendações do fabricante quanto ao tipo de lubrificante e à frequência de aplicação. A lubrificação adequada não apenas prolonga a vida útil do acoplamento, mas também melhora o desempenho do sistema como um todo.
4. Instalação Incorreta
A instalação incorreta do acoplamento é um erro que pode ter consequências graves. Um acoplamento mal instalado pode resultar em desalinhamento, folgas excessivas ou até mesmo danos aos componentes. Para evitar esse problema, é importante seguir as instruções do fabricante durante a instalação. Certifique-se de que os eixos estejam alinhados corretamente e que o acoplamento esteja montado de acordo com as especificações. Realizar testes de funcionamento após a instalação também é essencial para garantir que tudo esteja operando corretamente.
5. Ignorar Sinais de Desgaste
Ignorar sinais de desgaste nos acoplamentos é um erro que pode levar a falhas catastróficas. Durante as inspeções, é importante estar atento a sinais de desgaste, como rachaduras, folgas ou ruídos anormais. Se qualquer um desses sinais for identificado, é fundamental agir rapidamente, substituindo o acoplamento ou realizando os reparos necessários. A manutenção preventiva é essencial para evitar problemas maiores e garantir a segurança do sistema.
6. Não Realizar Manutenção Regular
A falta de manutenção regular é um erro que pode comprometer a eficiência e a durabilidade dos acoplamentos. Inspeções periódicas, limpeza e lubrificação são práticas essenciais que devem ser realizadas de acordo com um cronograma estabelecido. A manutenção regular ajuda a identificar problemas antes que se tornem críticos, prolongando a vida útil do acoplamento e evitando paradas inesperadas. É importante documentar todas as atividades de manutenção para garantir que nada seja esquecido.
7. Subestimar a Importância do Material do Acoplamento
Subestimar a importância do material do acoplamento é um erro que pode levar a falhas. Os acoplamentos são feitos de diferentes materiais, cada um com suas próprias propriedades e limitações. É fundamental escolher um material que seja adequado para as condições de operação, como temperatura, umidade e presença de contaminantes. Por exemplo, em ambientes corrosivos, acoplamentos feitos de materiais resistentes à corrosão são essenciais para garantir a durabilidade do sistema.
8. Não Considerar as Condições de Operação
Não considerar as condições de operação ao selecionar um acoplamento é um erro que pode resultar em falhas. Fatores como temperatura, umidade, vibrações e cargas dinâmicas devem ser levados em conta ao escolher o acoplamento. Ignorar essas condições pode levar a um desempenho inadequado e a um desgaste prematuro. É importante consultar as especificações do fabricante e garantir que o acoplamento escolhido seja adequado para as condições específicas de operação.
9. Falta de Treinamento da Equipe
A falta de treinamento da equipe responsável pela operação e manutenção dos equipamentos é um erro que pode resultar em problemas significativos. A equipe deve estar ciente das melhores práticas de instalação, manutenção e operação dos acoplamentos. Realizar treinamentos regulares e fornecer informações atualizadas sobre os procedimentos de manutenção é fundamental para garantir que todos estejam preparados para lidar com os desafios que podem surgir.
Em resumo, evitar erros comuns ao utilizar acoplamentos em redutores é essencial para garantir a eficiência e a durabilidade dos sistemas mecânicos. Desalinhamento dos eixos, escolha inadequada do tipo de acoplamento, falta de lubrificação, instalação incorreta, ignorar sinais de desgaste, não realizar manutenção regular, subestimar a importância do material, não considerar as condições de operação e falta de treinamento da equipe são erros que podem ser evitados com atenção e cuidado. Ao seguir as melhores práticas e estar atento a esses erros, você pode maximizar o desempenho dos acoplamentos e prolongar a vida útil dos equipamentos.
Em conclusão, a escolha e a manutenção adequadas do acoplamento para redutor são fundamentais para garantir a eficiência e a durabilidade dos sistemas mecânicos. Compreender os diferentes tipos de acoplamentos e suas aplicações, assim como evitar erros comuns durante a instalação e operação, pode resultar em um desempenho otimizado e na redução de custos operacionais. Ao seguir as melhores práticas discutidas, você estará melhor preparado para selecionar o acoplamento ideal e assegurar que seu sistema funcione de maneira confiável e segura ao longo do tempo.