Acoplamento Elástico de Garras: Como Escolher o Ideal
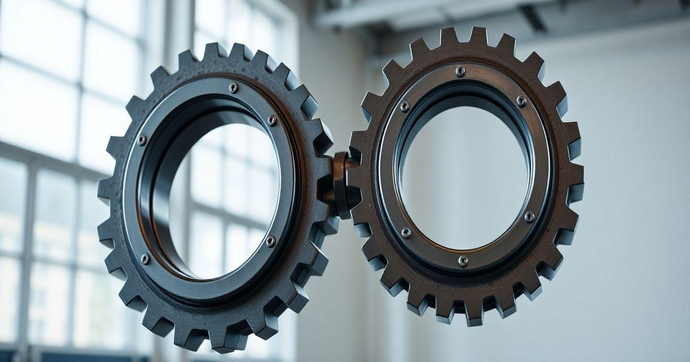
Por: Rodrigo - 25 de Dezembro de 2024
O acoplamento elástico de garras é um componente essencial em diversas aplicações industriais, proporcionando flexibilidade e eficiência na transmissão de potência. Neste artigo, vamos explorar o que é esse tipo de acoplamento, suas principais vantagens e como escolher o modelo ideal para suas necessidades. Se você deseja otimizar o desempenho de suas máquinas, continue lendo e descubra tudo sobre o acoplamento elástico de garras.
O que é o acoplamento elástico de garras
O acoplamento elástico de garras é um componente mecânico amplamente utilizado em sistemas de transmissão de potência, especialmente em maquinário industrial. Sua principal função é conectar dois eixos rotativos, permitindo a transmissão de torque enquanto absorve desalinhamientos e vibrações. Este tipo de acoplamento tem se tornado popular devido à sua capacidade de acomodar desalinhamentos angulares e axiais, o que resulta em uma operação mais suave e eficiente.
Um acoplamento elástico típico é composto por duas peças (ou garras) que se engatam em um elemento intermediário elástico. Este elemento, geralmente feito de borracha ou poliuretano, oferece as propriedades de amortecimento necessárias para absorver choques e reduzir vibrações. A elasticidade do material também permite que o acoplamento se ajuste a pequenas variações de alinhamento entre os eixos conectados, protegendo os componentes do sistema contra desgastes prematuros.
A construção do acoplamento elástico de garras é projetada para facilitar a montagem e a desmontagem, o que é uma vantagem significativa em ambientes industriais onde manutenção frequente é requerida. Além disso, sua estrutura simples e robusta oferece um custo-benefício atraente, tornando-o uma escolha popular para muitos engenheiros e técnicos.
Um aspecto importante do acoplamento elástico de garras é sua capacidade de balancear os eixos conectados. Quando os eixos estão desalinhados, forças não desejadas podem atuar sobre eles, levando a um desgaste excessivo e possíveis falhas mecânicas. O uso do acoplamento elástico minimiza esses problemas, assegurando que as forças aplicadas sejam distribuídas uniformemente e que o sistema opere de forma estável.
Os acoplamentos são utilizados em uma variedade de setores, incluindo automação industrial, energia, tratores e equipamentos de construção. Eles são frequentemente encontrados em motores elétricos, bombas, compressores e muitos outros dispositivos onde a transmissão de potência é essencial. Além disso, a versatilidade do acoplamento elástico de garras o torna aplicável em sistemas que enfrentam uma ampla gama de condições operacionais, desde operações leves até aplicações de alta carga.
Um ponto a ser destacado é que existem diferentes tipos de acoplamentos elásticos disponíveis no mercado, incluindo modelos bipartidos e outros variantes que atendem a necessidades específicas. O Acoplamento bipartido, por exemplo, é uma opção muito procurada devido à sua facilidade de instalação e manutenção, tornando-o uma escolha eficaz para muitos projetos.
É importante também considerar que, apesar de suas vantagens, o acoplamento elástico de garras deve ser escolhido com cuidado. Fatores como o tipo de aplicação, as condições de operação e as especificações dos eixos conectados devem ser levados em conta. A capacidade de torque, a rigidez do material e as dimensões são aspectos que devem ser avaliados para garantir a escolha correta do acoplamento.
Além disso, a instalação adequada do acoplamento elástico de garras é fundamental para seu funcionamento eficaz. Um alinhamento incorreto pode levar a desgastes prematuros e falhas no sistema. Portanto, recomenda-se que a instalação seja realizada por profissionais qualificados que entendam as nuances e os requisitos técnicos do processo.
Em resumo, o acoplamento elástico de garras é um componente crítico para a transmissão eficiente de potência em maquinário. Sua capacidade de absorver vibrações e acomodar desalinhamentos torna-o uma solução confiável em diversas aplicações industriais. Ao considerar o uso de um acoplamento elástico, é essencial escolher o modelo adequado e garantir uma instalação correta para maximizar sua eficiência e durabilidade.
Principais aplicações do acoplamento elástico de garras
O acoplamento elástico de garras é um componente versátil, amplamente utilizado em diversas indústrias devido à sua capacidade de realizar a transmissão de torque de maneira eficiente e flexível. Este tipo de acoplamento é projetado para atender a requisitos de desempenho em aplicações variadas, desde motores até sistemas complexos de automação. A seguir, exploraremos algumas das principais aplicações do acoplamento elástico de garras, destacando sua importância e benefícios em diferentes setores.
Um dos ambientes mais comuns para a aplicação do acoplamento elástico de garras é a indústria de fabricação. Máquinas industriais, como prensas, fresadoras e tornos, operam em condições que exigem uma conexão estável e eficiente entre os eixos. O acoplamento elástico de garras se destaca nesse cenário, pois pode lidar com desalinhamentos, absorvendo vibrações e garantindo um funcionamento suave da máquina. Isso não apenas aumenta a vida útil dos componentes, mas também melhora a qualidade do produto final.
No setor de petróleo e gás, os acoplamentos elásticos de garras são essenciais para garantir a confiabilidade dos equipamentos. Bombas, compressores e sensores utilizados em plataformas petrolíferas frequentemente empregam esse tipo de acoplamento. Com condições operacionais desafiadoras, como temperaturas extremas e alta pressão, a capacidade do acoplamento de suportar vibrações e desalinhamientos se torna crucial para o funcionamento seguro e eficaz dos sistemas.
A indústria de energia também se beneficia do acoplamento elástico de garras. Em geradores, turbinas eólicos e outros sistemas de geração de energia, esses acoplamentos ajudam a minimizar a transmissão de vibrações indesejadas que poderiam comprometer a eficiência do sistema. A flexibilidade oferecida por eles é especialmente valiosa em instalações onde mudanças de carga são frequentes, permitindo um melhor desempenho enquanto se mantém a integridade dos componentes envolvidos.
Outro campo de aplicação importante é a automação industrial. Em sistemas robóticos, transportadores e máquinas de montagem, o acoplamento elástico de garras possibilita a conexão entre motores e atuadores, permitindo o movimento preciso das partes móveis. A elasticidade do material do acoplamento reduz a carga sobre os motores e mecanismos, contribuindo para um funcionamento mais eficiente e com menor consumo de energia.
Os acoplamentos elásticos de garras também são usados em veículos e maquinário pesado. Em tratores, escavadeiras e outras máquinas de construção, eles conectam motores a sistemas de transmissão, permitindo que o torque seja transferido de maneira eficaz, mesmo em condições de trabalho severas. A resistência a choques e vibrações é vital nesse contexto, uma vez que o terreno e as cargas podem variar amplamente, exigindo flexibilidade e adaptabilidade.
Além disso, o acoplamento elástico de garras é utilizado em sistemas de produção de alimentos e bebidas. Máquinas de envase, misturadores e transportadoras frequentemente utilizam esses componentes para garantir que os ingredientes sejam movimentados de forma eficiente e precisa. A capacidade do acoplamento de absorver vibrações e choques garante que os produtos possam ser processados sem comprometer a qualidade e segurança alimentar.
Os acoplamentos elásticos de garras também podem ser encontrados em aplicações de ventilação e climatização. Os sistemas de ventiladores e compressores de ar usam este tipo de acoplamento para garantir que a energia seja transferida de forma eficiente, mantendo o conforto e a segurança em ambientes industriais e comerciais. Aqui, o controle de vibrações é crucial para manter a operação silenciosa e eficaz dos equipamentos.
Por último, a comparação entre o acoplamento elástico de garras e outras soluções de acoplamento, como o acoplamento elástico de pinos, evidencia a flexibilidade e versatilidade das garras. Cada tipo de acoplamento apresenta características únicas que atendem a diferentes necessidades, reforçando a importância de entender seu funcionamento e aplicações para fazer a escolha certa para cada projeto.
Em resumo, o acoplamento elástico de garras é uma solução eficaz em diversas indústrias, ajudando a melhorar a eficiência operacional, aumentar a durabilidade dos sistemas e minimizar custos de manutenção. A versatilidade desses acoplamentos faz deles uma escolha popular em ambientes industriais, onde a confiabilidade e a performance são cruciais para o sucesso das operações.
Vantagens do acoplamento elástico de garras
O acoplamento elástico de garras é amplamente utilizado em diversas indústrias devido às suas propriedades que promovem eficiência e confiabilidade em sistemas de transmissão de potência. As vantagens desse tipo de acoplamento são responsáveis por sua popularidade em aplicações mecânicas, destacando-se pela capacidade de solução em diversos desafios operacionais. Neste artigo, são apresentadas as principais vantagens do acoplamento elástico de garras, que o tornam uma escolha ideal para muitas aplicações industriais.
Uma das principais vantagens do acoplamento elástico de garras é sua capacidade de absorver vibrações. Em sistemas onde a transmissão de torque é fundamental, a presença de vibrações pode ser prejudicial, levando a um desgaste acelerado dos componentes e, consequentemente, a falhas mecânicas. Graças à construção de materiais elásticos, esses acoplamentos conseguem minimizar a transmissão de vibrações, proporcionando um funcionamento mais suave e controlado. Isso se traduz em menor desgaste, aumentando a vida útil dos equipamentos conectados.
Além de absorver vibrações, o acoplamento elástico de garras também é eficaz em acomodar desalinhamentos. Desalinhamentos entre eixos são comuns em sistemas rotativos e podem ocorrer devido a condições de operação, instalação inadequada ou desgaste das peças. O acoplamento elástico permite certa liberdade de movimento, ajustando-se aos desalinhamentos axiais e angulares sem comprometer a transmissão de torque. Isso ajuda a evitar danos aos componentes e a garantir um desempenho contínuo e eficiente do sistema.
Outro ponto positivo é a facilidade de instalação e manutenção. O desenho simples dos acoplamentos elásticos de garras torna a montagem e desmontagem um processo direto e rápido. Isso é particularmente importante em ambientes industriais onde a redução do tempo de inatividade é crucial para a produtividade. Além disso, a manutenção é facilitada, pois o acesso aos eixos conectados é mais descomplicado, ajudando a manter os sistemas em operação e reduzindo os custos associados a paradas e reparos.
O custo-benefício do acoplamento elástico de garras é outro aspecto a ser mencionado. Os materiais utilizados em sua fabricação apresentam uma relação custo-efetividade favorável, especialmente quando comparados a outros tipos de acoplamentos, como o Acoplamento De Pino. O investimento inicial em um acoplamento elástico pode ser menor, mas as economias em manutenção e operação a longo prazo o tornam uma opção bastante viável para muitas empresas. Com a redução das falhas e a necessidade de manutenção, o retorno sobre o investimento se torna significativo.
A versatilidade do acoplamento elástico de garras é uma característica que merece destaque. Ele pode ser utilizado em uma ampla gama de aplicações, desde sistemas de transmissão de energia em máquinas pesadas até pequenas ferramentas elétricas. Essa diversidade de aplicação é uma das razões pelas quais ele é frequentemente escolhido em projetos industriais, pois pode atender a diferentes requisitos de performance e eficiência.
Outro benefício importante é a capacidade de lidar com mudanças de carga e condições operacionais. O acoplamento elástico de garras se adapta facilmente a variações na carga e às solicitações dinâmicas do sistema. Isso é particularmente relevante em ambientes onde as condições de trabalho podem mudar abruptamente, garantindo que o sistema permaneça funcional e confiável sob diferentes circunstâncias. Essa adaptabilidade contribui para a estabilidade do desempenho ao longo do tempo.
Por fim, a redução do ruído também é uma vantagem significativa associada ao uso do acoplamento elástico de garras. Com a habilidade de absorver as vibrações e minimizar as forças de impacto entre os componentes mecânicos, esses acoplamentos ajudam a criar um ambiente de trabalho mais silencioso. Isso não só melhora as condições de trabalho, mas também contribui para a conformidade com regulamentações de segurança e saúde ocupacional.
Em conclusão, as vantagens do acoplamento elástico de garras são inegáveis. Sua capacidade de absorver vibrações, acomodar desalinhamentos e proporcionar facilidade de instalação e manutenção faz dele uma escolha prática e eficiente para diversos setores. A relação custo-benefício e a versatilidade, junto com a habilidade de lidar com mudanças de carga e reduzir ruído, fazem do acoplamento elástico de garras uma solução confiável e essencial em aplicações industriais. Ao considerar os requisitos de um projeto, as empresas são incentivadas a explorar as possibilidades oferecidas pelo acoplamento elástico de garras para garantir um desempenho ideal e minimizar custos operacionais ao longo da vida útil do equipamento.
Como funciona o acoplamento elástico de garras
O acoplamento elástico de garras é um dispositivo mecânico projetado para conectar eixos rotativos em sistemas de transmissão de potência. Sua principal função é transmitir torque entre os eixos enquanto oferece certas características de flexibilidade e absorção de vibrações. Mas como exatamente funciona este tipo de acoplamento e quais são os princípios por trás de sua operação? Neste artigo, vamos explorar os componentes do acoplamento elástico de garras, seu funcionamento e os benefícios que ele traz a aplicações industriais.
No centro do funcionamento do acoplamento elástico de garras está o seu design. Este tipo de acoplamento é composto por duas garras que se interligam por um elemento elástico, geralmente feito de borracha ou poliuretano. As garras são ligadas a cada eixo, criando uma conexão rígida e ao mesmo tempo flexível. O elemento elástico entre as garras e os eixos é o que permite que o acoplamento absorva vibrações e desalinhamentos. Essa construção evita que forças excessivas sejam transmitidas entre os eixos, minimizando o risco de falhas mecânicas.
Quando um motor, por exemplo, está acionado, o torque gerado por ele deve ser transmitido ao próximo eixo. Nesse momento, o acoplamento elástico de garras entra em ação. Quando os eixos estão perfeitamente alinhados, o torque é transmitido diretamente. Contudo, na prática, pequenas variações no alinhamento podem ocorrer. É aqui que a elasticidade do material entra em jogo. O acoplamento permite que as garras se movam de maneira independente, proporcionando uma margem de manobra que adapta-se às variações de ângulo e distância entre os eixos. Essa característica é fundamental, pois ajuda a prolongar a vida útil dos componentes envolvidos.
Além disso, a capacidade do acoplamento de absorver vibrações proporciona um funcionamento mais estável. Quando há um desvio, como em situações de choque ou sobrecarga, a energia excessiva é dissipada pelo material elástico entre as garras, reduzindo a intensidade das forças transmitidas entre os eixos. Isso ajuda a prevenir desgastes e falhas nos componentes rotativos, contribuindo para uma operação mais confiável.
A instalação de um acoplamento elástico de garras é relativamente simples. Os usuários devem garantir que os eixos estejam alinhados conforme recomendado, mas o próprio acoplamento apresenta uma tolerância de desalinhamento, facilitando a operação. Uma vez instalado, a manutenção é geralmente baixa, pois não requer ajustes frequentes ou substituições, a menos que o material elástico comece a apresentar sinais de desgaste.
Uma das vantagens importantes dos acoplamentos elásticos de garras é a sua aplicação em uma ampla gama de indústrias e sistemas de máquinas. O acoplamento se adapta a várias configurações e requisitos de torque, permitindo sua utilização em tudo, desde pequenas ferramentas elétricas até enormes máquinas industriais. Este tipo de acoplamento pode ser encontrado em sistemas de transmissão onde o controle de vibrações é crítico, como em bombas, motores, ventiladores, compressores e até mesmo em equipamentos de transporte.
Outra característica interessante é que, assim como o acoplamento elástico de garras, existem diversos outros modelos de acoplamentos disponíveis no mercado, incluindo o Acoplamento omega, que oferece características específicas adaptadas a determinadas aplicações. A escolha do tipo apropriado de acoplamento é fundamental para garantir um desempenho ideal nas máquinas.
É importante ressaltar que a instalação e o funcionamento adequados do acoplamento elástico de garras dependem não apenas de sua construção, mas também da compreensão das forças e necessidades operacionais da aplicação específica. Mesmo que o acoplamento forneça flexibilidade e propriedades de absorção de vibrações, um entendimento claro dos aspectos técnicos envolvidos na sua aplicação é necessário para maximizar seu desempenho e durabilidade.
Por fim, a inovação na fabricação de acoplamentos elásticos de garras continua a evoluir, com novos materiais e designs sendo desenvolvidos para atender às exigências cada vez maiores das indústrias modernas. A pesquisa e o desenvolvimento nessas áreas têm o potencial de oferecer soluções ainda mais eficientes, ampliando o escopo de aplicação e a eficácia desses dispositivos. À medida que as demandas por melhor desempenho e eficiência aumentam, o papel dos acoplamentos elásticos de garras se tornará ainda mais central nas engenharias de movimentação de potência.
Em resumo, o acoplamento elástico de garras funciona como um importante mediador na transmissão de torque entre eixos rotativos. Seu design inovador, que combina garras rígidas a um elemento elástico, permite uma operação flexível e eficiente, garantindo que as forças sejam geridas com eficácia, prolongando a vida útil dos sistemas aos quais são integrados. Seja em máquinas pesadas ou equipamentos mais leves, entender como esse acoplamento opera é essencial para otimizar seu desempenho e garantir resultados satisfatórios em qualquer aplicação industrial.
Critérios para escolher o acoplamento elástico de garras
Escolher o acoplamento elástico de garras correto é um passo fundamental para garantir a eficiência e a durabilidade dos sistemas mecânicos em que será aplicado. Existem várias considerações e critérios a serem levados em conta durante esse processo decisório. A seguir, discutiremos os principais critérios que devem ser avaliados ao selecionar um acoplamento elástico de garras, assegurando que ele atenda às necessidades específicas da sua aplicação.
Um dos primeiros critérios a considerar é a capacidade de torque. Cada acoplamento possui uma classificação que indica a quantidade de torque que pode ser transmitido sem falhas. É crucial que a capacidade de torque do acoplamento escolhido seja adequada para a aplicação em questão, levando em conta a carga máxima que será imposta. Se o torque exceder a capacidade do acoplamento, isso pode levar a falhas mecânicas, danos aos equipamentos e custos adicionais de manutenção.
Outro ponto importante é o tipo de alinhamento que será encontrado na aplicação. Os acoplamentos elásticos de garras são projetados para acomodar desalinhamentos angulares e axiais, mas a extensão dessa tolerância varia entre os modelos. Ao considerar o alinhamento, avalie quão crítico é o alinhamento preciso entre os eixos em sua aplicação. Se houver grandes variações nas condições de operação, um acoplamento com maior capacidade de desalinhamento pode ser necessário.
A rigidez do material utilizado no acoplamento é outro aspecto que deve ser considerado. A rigidez influencia a capacidade do acoplamento de transmitir torque, bem como a quantidade de vibração que poderá ser absorvida. Materiais mais rígidos podem oferecer melhor desempenho em aplicações que exigem alta precisão, enquanto materiais mais flexíveis proporcionam melhor capacidade de absorção de choques e vibrações. A escolha do material deve ser baseada nas condições operacionais e nas necessidades específicas do sistema.
A temperatura também deve ser levada em conta ao escolher um acoplamento elástico de garras. Diferentes materiais têm diferentes limites de temperatura, e expor um acoplamento a temperaturas superiores ao recomendado pode causar falhas no material, levando a danos ao acoplamento e ao sistema conectado. É fundamental conhecer a faixa de temperatura operacional do ambiente em que a aplicação ocorrerá e selecionar um acoplamento que seja adequado para essas condições.
O tamanho e as dimensões do acoplamento também devem ser analisados. Um acoplamento inadequadamente dimensionado pode resultar em dificuldades de instalação ou funcionamento. É essencial considerar o espaço disponível para a instalação do acoplamento, bem como as dimensões dos eixos que ele conectará. Um dimensionamento correto garantirá um encaixe adequado e ajudará a evitar problemas de desempenho.
Além disso, a manutenção e a durabilidade dos acoplamentos são aspectos que merecem atenção. Escolher um acoplamento que necessite de pouca manutenção e que tenha uma vida útil prolongada é um objetivo desejável. A maioria dos acoplamentos elásticos de garras requer manutenção mínima, mas é importante verificar quaisquer recomendações do fabricante e considerar como a manutenção se alinha com as práticas operacionais do seu sistema.
O custo também é um fator a ser considerado na escolha do acoplamento elástico de garras. Embora o preço não deva ser o único critério, é importante ter em mente a relação custo-benefício. Acoplamentos de qualidade superior podem ter um custo inicial mais elevado, mas podem resultar em economia de custos a longo prazo, devido à menor frequência de falhas e manutenção. Avalie os diferentes modelos no mercado e considere qual opção oferece o melhor retorno sobre o investimento.
Por último, mas não menos importante, a reputação e a confiabilidade do fabricante são fatores que não devem ser ignorados. Optar por marcas reconhecidas e que têm um histórico comprovado de produção de acoplamentos de qualidade pode reduzir significativamente os riscos associados a falhas mecânicas. Pesquise referências e analise opiniões de outros usuários sobre o desempenho dos acoplamentos que você está considerando.
Em resumo, ao escolher um acoplamento elástico de garras, a avaliação cuidadosa de critérios como capacidade de torque, tipo de alinhamento, rigidez do material, temperatura, tamanho e dimensões, manutenção, custo e confiabilidade do fabricante é fundamental. Esses fatores contribuirão para a seleção do acoplamento mais adequado para sua aplicação, garantindo a eficiência e a confiabilidade do sistema ao longo do tempo. Tomar decisões informadas durante esse processo pode resultar em uma operação mais suave, menor desgaste e custos reduzidos no que diz respeito à manutenção e ao tempo de inatividade.
Tipos de acoplamento elástico de garras disponíveis
Os acoplamentos elásticos de garras são dispositivos fundamentais para a transmissão de torque em sistemas mecânicos, e sua escolha pode variar amplamente dependendo das necessidades específicas de cada aplicação. No mercado, existem diferentes tipos de acoplamentos elásticos de garras disponíveis, cada um com características próprias que atendem a diversas exigências operacionais. A seguir, discutiremos os principais tipos de acoplamentos elásticos de garras disponíveis, suas especificações e as aplicações mais adequadas para cada um deles.
Um dos tipos mais comuns de acoplamento elástico de garras é o acoplamento de plástico. Este modelo é usado em uma variedade de aplicações onde a leveza e a resistência à corrosão são preocupações principais. Feitos de materiais plásticos industriais, como nylon ou poliuretano, eles oferecem boa resistência ao desgaste e podem ser utilizados em ambientes úmidos ou com presença de produtos químicos. O acoplamento de plástico é ideal para motores elétricos menores, impressoras e equipamentos médicos, onde o peso e a corrosão são fatores críticos.
Outro tipo amplamente utilizado é o acoplamento de aço inoxidável. Este modelo é projetado para aplicações que exigem resistência a ambientes agressivos ou corrosivos, como indústrias químicas e alimentícias. Os acoplamentos de aço inoxidável são robustos e oferecem excelente resistência à corrosão, tornando-os ideais para operações onde a higienização é crucial. Além disso, sua durabilidade acrescenta segurança e confiabilidade ao sistema, atendendo a uma ampla gama de exigências industriais.
O acoplamento de garras de alumínio também é uma opção notável no mercado. Combinando leveza e resistência, esses acoplamentos em alumínio são projetados para aplicações onde a redução de peso é prioritária, como em equipamentos móveis e robóticos. Sua estrutura leve permite uma aceleração mais rápida e eficiência energética, além de ser uma solução eficaz para sistemas que exigem alta performance. Eles são frequentemente utilizados em automação industrial e engenharia mecânica.
Os acoplamentos de garras flexíveis são outros exemplos que demonstram versatilidade. Esses acoplamentos são projetados para acomodar desalinhamentos angulares e radiais, permitindo um maior grau de flexibilidade. Feitos geralmente de borracha, esses acoplamentos são ideais para equipamentos industriais que podem sofrer vibrações ou choques, como compressores e bombeamento de fluidos. Sua capacidade de dissipar energia faz deles uma escolha popular em diversas aplicações, incluindo máquinas pesadas e equipamentos de construção.
Um modelo a destacar são os acoplamentos de garras bipartidos, que oferecem uma abordagem distinta para aplicações que requerem fácil manutenção e instalação. Com um design que permite a separação das garras, esses acoplamentos são ideais para sistemas onde é necessário realizar manutenção regularmente, como em transportadores e sistemas de produção. A facilidade de instalação e acesso aos componentes aumenta a eficiência da manutenção, reduzindo o tempo de inatividade e os custos operacionais.
Os acoplamentos de garras de alta velocidade são projetados para operações que exigem desempenho em altas rotações. Eles são construídos para suportar estresse adicional e forças centrífugas geradas em aplicações de alta velocidade, como turbinas e geradores. Os materiais utilizados nestes acoplamentos são muitas vezes tratados para resistir a fadiga e desgaste, garantindo a integridade do sistema mesmo sob condições extremas. Isso os torna essenciais em ambientes industriais que exigem precisão e alta eficiência.
Outro tipo considerável são os acoplamentos de garras hidráulicos. Esse tipo é ideal para aplicações onde a transferência de potência e a suavidade operacional são essenciais. Projetados especificamente para sistemas hidráulicos, esses acoplamentos oferecem uma combinação de flexibilidade e rigidez, o que permite que o sistema opere de maneira eficiente mesmo em condições de carga variável. Eles são frequentemente utilizados em máquinas de construção, onde a força e o controle são fundamentais.
Por último, não podemos deixar de mencionar os acoplamentos de garras antirruído. Esses modelos são projetados para oferecer recursos adicionais destinados a minimizar o ruído e a vibração durante a operação. Comumente utilizados em aplicações que exigem operações silenciosas, como em ambientes hospitalares ou na indústria de alimentos, sua capacidade de atenuar ruídos e transmitir torque de forma eficaz os torna uma escolha popular para diversas indústrias.
Em resumo, a diversidade de tipos de acoplamento elástico de garras disponíveis no mercado garante que haja uma opção adequada para praticamente qualquer aplicação. Sejam os acoplamentos de plástico, aço inoxidável, alumínio ou qualquer um dos vários modelos específicos, entender as características e benefícios de cada tipo é crucial para selecionar o acoplamento mais eficiente e confiável para suas necessidades industriais. A escolha apropriada não só garante a eficiência operacional, mas também prolonga a vida útil dos componentes envolvidos, resultando em um excelente retorno sobre o investimento.
Instalação e manutenção do acoplamento elástico de garras
A instalação e a manutenção adequadas do acoplamento elástico de garras são essenciais para garantir o desempenho eficiente e a longevidade do equipamento em que ele é utilizado. Embora esse tipo de acoplamento seja projetado para ser simples e eficaz, seguir as diretrizes corretas durante a instalação e a manutenção pode evitar problemas futuros e assegurar que o sistema funcione de maneira otimizada. Neste artigo, abordaremos as etapas recomendadas para a instalação e os cuidados necessários na manutenção dos acoplamentos elásticos de garras.
Para começar, a instalação de um acoplamento elástico de garras exige atenção ao alinhamento dos eixos que serão conectados. Um dos passos mais importantes antes de instalar o acoplamento é verificar se os eixos estão adequadamente alinhados. Desalinhamentos podem causar desgaste excessivo e falhas nos componentes. Para tanto, é aconselhável utilizar ferramentas de medição, como alinhadores a laser, que garantem um alinhamento preciso, minimizando a probabilidade de problemas futuros.
Após garantir que os eixos estejam alinhados, a próxima etapa é montar o acoplamento. Geralmente, a instalação envolve prender um lado do acoplamento em um eixo e, em seguida, o outro lado no eixo adjacente. Certifique-se de que o acoplamento esteja firmemente preso e que as garras estejam engatadas corretamente no elemento elástico. É fundamental seguir as especificações do fabricante quanto aos torque de aperto, pois um aperto excessivo pode danificar as peças.
Além disso, o ajuste da folga axial é um passo que não deve ser negligenciado. Uma folga excessiva pode resultar em vibrações indesejadas, enquanto uma folga insuficiente pode causar atrito e aquecimento. Por isso, os fabricantes frequentemente fornecem especificações detalhadas sobre a folga de instalação, que deve ser seguida rigorosamente durante o processo. A correta definição da folga axia também contribui para a eficiência do sistema, maximizando a transmissão de torque.
Depois de concluir a instalação, é essencial realizar um teste de funcionamento. Ligue o sistema e observe o comportamento do acoplamento durante a operação. Verifique se há vibrações, ruídos ou aquecimentos anormais. Se algum problema for detectado, pode ser necessário desligar o sistema e revisar a instalação. Isso é crucial para evitar danos subsequentes ao equipamento e garantir que tudo esteja funcionando conforme esperado.
Agora que a instalação está concluída, é hora de discutir a manutenção. Embora os acoplamentos elásticos de garras sejam projetados para requerer pouca manutenção, alguns cuidados regulares são essenciais para garantir sua durabilidade e eficiência a longo prazo. Uma das práticas mais importantes é a inspeção periódica. É recomendável verificar o acoplamento periodicamente em busca de sinais de desgaste, como rachaduras no material elástico ou folga excessiva. Esse tipo de inspeção ajuda a identificar problemas antes que se tornem críticos, minimizando o risco de falhas operacionais.
A limpeza regular do acoplamento e dos componentes adjacentes também é uma parte importante da manutenção. Acúmulos de sujeira, pó e detritos podem interferir no funcionamento suave do acoplamento. Utilize produtos de limpeza apropriados e evite o uso de solventes agressivos que possam danificar os materiais. A limpeza periódica garante que os componentes do sistema mantenham sua integridade e operem da melhor forma possível.
Além disso, deve-se prestar atenção à lubrificação, quando necessário. Embora muitos acoplamentos elásticos de garras não exijam lubrificação, alguns modelos podem ter partes que se beneficiam de lubrificantes específicos. Consulte as recomendações do fabricante para verificar se é necessário aplicar lubrificação e qual o tipo ideal para cada aplicação. A lubrificação correta ajuda a reduzir o atrito e o desgaste entre os componentes, prolongando a vida útil do acoplamento.
Para garantir que o acoplamento continue funcionando perfeitamente, é fundamental também realizar ajustes regulares. As condições operacionais podem mudar ao longo do tempo, portanto, ajustes podem ser necessários para adequar a configuração do acoplamento às novas exigências. Isso pode incluir a verificação e o ajuste do alinhamento, da folga axial e do torque de aperto, conforme indicado pelas especificações do fabricante.
Por fim, em caso de falhas ou desgastes significativos, pode ser necessário realizar a substituição do acoplamento. Novamente, recomenda-se seguir as especificações do fabricante quanto ao tempo de vida útil do componente e as condições de operação. Utilizar um acoplamento desgastado pode resultar em quebra ou falha catastrófica do sistema, causando não apenas prejuízos financeiros, mas também riscos à segurança no ambiente de trabalho.
Em resumo, a instalação e manutenção do acoplamento elástico de garras são fundamentais para garantir um funcionamento eficiente e prolongar a vida útil do equipamento. Ao seguir as diretrizes adequadas para a instalação e se comprometer com uma manutenção regular, é possível maximizar a eficiência do sistema e minimizar riscos de falhas. Assim, com cuidado e atenção aos detalhes, qualquer operação que envolva acoplamentos elásticos de garras pode ser realizada com sucesso, contribuindo para a eficiência e confiabilidade das máquinas industriais.
Erros comuns ao utilizar acoplamento elástico de garras
O acoplamento elástico de garras é um componente mecânico amplamente utilizado em sistemas de transmissão de potência, oferecendo flexibilidade e eficiência na conexão entre eixos rotativos. No entanto, sua eficácia pode ser comprometida por uma série de erros comuns em sua utilização e instalação. Neste artigo, abordaremos alguns dos principais erros que podem ocorrer ao utilizar acoplamentos elásticos de garras e como evitá-los, assegurando que o sistema opere de forma otimizada e confiável.
Um dos primeiros erros que podem ser cometidos é a falta de alinhamento adequado dos eixos durante a instalação do acoplamento. O desalinhamento entre os eixos é uma das principais causas de falhas em sistemas que utilizam acoplamentos. Quando os eixos não estão corretamente alinhados, pode-se resultar em forças excessivas que são transmitidas pelo acoplamento, levando a desgastes prematuros e diminuindo sua vida útil. É vital utilizar ferramentas de medição adequadas, como alinhadores a laser, para garantir um alinhamento preciso, minimizando problemas que possam surgir devido a desalinhamentos conativos ou axiais.
Outro erro comum é não considerar a folga axial necessária entre os eixos durante a instalação. A folga axial excessiva ou insuficiente pode causar vibrações, ruídos e até mesmo falhas no acoplamento. Sempre consulte as especificações do fabricante para garantir que a folga axial esteja de acordo com as recomendações. O ajuste correto dessa folga é crucial para o desempenho ideal do acoplamento e contribui para a estabilidade da operação.
A aplicação inadequada de torque nos parafusos de fixação que conectam o acoplamento aos eixos também é uma fonte comum de problemas. Um aperto excessivo pode causar deformações ou danos ao material do acoplamento, enquanto um aperto insuficiente pode resultar em folgas e desconexões durante a operação. É recomendável seguir as especificações do fabricante quanto ao torque de aperto, garantindo que todos os parafusos estejam firmemente fixados, mas sem aplicar força excessiva que possa comprometer a integridade do material.
Além disso, a negligência na manutenção preventiva é um erro frequentemente observado. Embora os acoplamentos elásticos de garras sejam projetados para requerer pouca manutenção, é essencial realizar inspeções periódicas para identificar sinais de desgaste, como rachaduras no material elástico ou folga excessiva. Ignorar a manutenção regularmente pode levar a problemas não detectados, que podem resultar em falhas catastróficas. O custo e o tempo gasto em uma manutenção preventiva são sempre menores em comparação com os custos de reparos e substituições após uma falha.
Outro erro relacionado à manutenção é a falta de limpeza adequada do acoplamento e dos componentes adjacentes. Acúmulos de sujeira, poeira e detritos podem interferir no funcionamento suave do acoplamento, resultando em atritos e desgastes indesejados. É fundamental realizar limpezas regulares usando produtos apropriados, evitando solventes agressivos que possam danificar os materiais do acoplamento. A limpeza regular ajuda a manter a integridade do sistema e garante que os componentes operem da melhor forma possível.
A escolha inadequada do tipo de acoplamento para uma aplicação específica é outro erro que não pode ser subestimado. Existem diversos tipos de acoplamentos elásticos de garras projetados para atender a diferentes necessidades e condições operacionais, como temperatura, carga e ambiente. Ao selecionar um acoplamento, é crucial considerar as especificações e as exigências da aplicação. Um acoplamento inadequado pode falhar rapidamente sob condições de carga e ambiente inadequados. Conhecer as opções disponíveis e suas características é essencial para um desempenho eficaz.
Outro erro comum é a não verificação de compatibilidade entre materiais. O material utilizado para o acoplamento deve ser compatível com os elementos que ele conecta. Por exemplo, a interação entre materiais metálicos e plásticos ou borrachas pode resultar em reações químicas que comprometam a integridade do acoplamento. É essencial avaliar as propriedades dos materiais e garantir que eles sejam compatíveis, evitando possíveis falhas devido a degradações prematuras.
Além disso, a negligência na avaliação das condições operacionais é um erro que muitos cometem. Fatores como temperatura, pressão e vibrações devem ser considerados para que o acoplamento escolhido caminha dentro das especificações adequadas. A falta de consideração das condições operacionais pode levar a falhas no acoplamento, resultando em paradas indesejadas e custos associados a manutenção. Conhecer e controlar essas variáveis ajuda a garantir o funcionamento correto do sistema.
Por fim, a falta de documentação e registros sobre a instalação e manutenção do acoplamento é um erro que pode dificultar a resolução de problemas no futuro. Manter registros detalhados sobre inspeções, manutenções e substituições ajuda a identificar padrões de falhas e a otimizar o desempenho do sistema. Essa documentação também pode ser útil para auditorias e para garantir a conformidade com padrões de segurança e qualidade.
Em resumo, evitar os erros comuns ao utilizar acoplamento elástico de garras é fundamental para garantir um desempenho eficiente e a longevidade dos sistemas mecânicos. Desde a instalação correta até a manutenção periódica, cada passo deve ser realizado com atenção e cuidado para evitar problemas que possam comprometer toda a operação. Seguir as diretrizes adequadas e estar atento às práticas recomendadas ajudará a maximizar a performance e minimizar os riscos associados ao uso de acoplamentos elásticos de garras, contribuindo para a eficiência e confiabilidade do maquinário industrial.
Em conclusão, o acoplamento elástico de garras desempenha um papel fundamental na eficiência operacional de diversas indústrias. Com suas características únicas, como a capacidade de absorver vibrações e acomodar desalinhamentos, esse tipo de acoplamento se destaca como uma solução versátil e confiável para a transmissão de potência. Ao longo deste artigo, discutimos não apenas o que é o acoplamento elástico de garras, mas também as suas vantagens, critérios de escolha, tipos disponíveis, aspectos de instalação e manutenção, além de erros comuns que devem ser evitados. Com esse conhecimento, você está melhor preparado para selecionar o acoplamento ideal para suas necessidades específicas e otimizar o desempenho das suas máquinas, garantindo maior durabilidade e eficiência em suas operações. Investir em acoplamentos de qualidade, juntamente com práticas adequadas de instalação e manutenção, é essencial para manter a produtividade e a eficácia dos processos industriais.