Acoplamento de Garras: Tudo que Você Precisa Saber
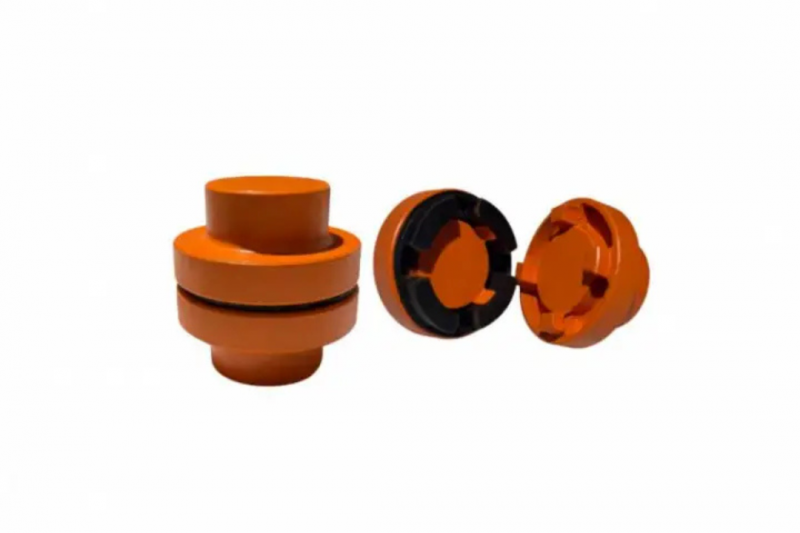
Por: Rodrigo - 25 de Dezembro de 2024
Acoplamento de garras é um componente essencial na transmissão de torque em diversas aplicações industriais. Neste artigo, abordaremos o que é o acoplamento de garras, seus diferentes tipos e as vantagens que oferece. Além disso, você aprenderá como escolher o modelo ideal, suas aplicações comuns e os cuidados necessários para garantir seu funcionamento eficiente. Continue lendo e descubra como esse essencial pode melhorar sua operação industrial.
O que é Acoplamento de Garras
O acoplamento de garras é um dispositivo utilizado para conectar dois eixos rotativos, permitindo a transmissão de torque entre eles. Ele é projetado para unir de forma eficiente motores e outros componentes rotativos, garantindo um funcionamento suave e eficiente do sistema. Composto por três partes principais – duas garras e um corpo – esse tipo de acoplamento oferece uma combinação de funcionalidade, durabilidade e eficiência.
Um dos principais benefícios do acoplamento de garras é a sua capacidade de acomodar desalinhamentos angulares e radiais. Isso significa que, mesmo que os eixos não estejam perfeitamente alinhados, o acoplamento pode compensar essa diferença, evitando desgaste excessivo e falhas que poderiam comprometer o funcionamento do sistema. A flexibilidade do acoplamento de garras se torna ainda mais evidente em aplicações industriais, onde as condições de operação podem variar consideravelmente.
Os acoplamentos de garras são amplamente utilizados em várias indústrias, como a de automação, transporte e mesmo na indústria alimentícia. Sua aplicação se dá, principalmente, em máquinas que requerem a transmissão de potência entre eixos, como esteiras transportadoras, bombas e misturadores, devido à sua eficiência na transferência de força sem perda de energia significativa.
Este tipo de acoplamento é projetado para suportar altas cargas e forças, tornando-se uma escolha ideal para aplicações que exigem robustez e confiabilidade. O material das garras e do corpo do acoplamento é geralmente um metal de alta resistência, o que contribui para a durabilidade e a vida útil do dispositivo. Além disso, o acoplamento pode ser projetado para ser leve, facilitando a instalação e o manuseio durante operações de manutenção.
Outra característica importante do acoplamento de garras é a sua capacidade de absorver choques e vibrações. Em ambientes industriais, as máquinas frequentemente sofrem impactos e situações de estresse que podem afetar sua performance. O acoplamento de garras, projetado com máquinas de alta precisão, pode minimizar esses impactos, proporcionando um funcionamento mais suave e diminuindo o potencial de falhas mecânicas.
Os diferentes tipos de acoplamentos de garras disponíveis no mercado também oferecem versatilidade. Alguns são projetados para aplicações específicas, enquanto outros podem ser utilizados em uma ampla gama de sistemas. Isso permite que os engenheiros escolham o modelo mais adequado com base nas necessidades específicas de cada projeto, considerando fatores como torque, velocidade e alinhamento.
Um bom exemplo de uma variação do acoplamento de garras é o Acoplamento bipartido , que se destaca por sua facilidade de montagem e manutenção, além de proporcionar uma excelente capacidade de alinhamento. Essa opção é frequentemente escolhida por aplicações onde o espaço é limitado, mas ainda assim é necessário garantir uma conexão resistente e confiável entre os eixos.
Uma preocupação comum entre os profissionais que utilizam acoplamentos de garras é a questão do desgaste. É importante realizar manutenções periódicas e inspeções para garantir que os componentes se mantenham em bom estado, evitando que pequenos danos se tornem problemas maiores. A substituição de peças desgastadas, como garras, pode prolongar a vida útil do acoplamento e do sistema como um todo.
Em resumo, o acoplamento de garras é uma solução eficaz e versátil para a transmissão de torque entre eixos em aplicações industriais. Sua capacidade de acomodar desalinhamentos, absorver choques e vibrar e oferecer uma transmissão eficiente faz dele uma opção popular entre engenheiros e técnicos. Com a variedade de modelos disponíveis, é possível encontrar um acoplamento que atenda às necessidades específicas de cada projeto, garantindo um funcionamento eficiente e confiável.
Tipos de Acoplamento de Garras
Os acoplamentos de garras são dispositivos cruciais em muitas aplicações industriais, e existem diferentes tipos projetados para atender a necessidades específicas. Cada tipo de acoplamento de garras possui características únicas que proporcionam vantagens em determinadas situações. Neste artigo, exploraremos os principais tipos de acoplamento de garras, suas aplicações e benefícios.
Um dos tipos mais comuns é o acoplamento de garras metálicas. Este modelo é feito de materiais metálicos de alta resistência, permitindo que ele suporte cargas pesadas e altas velocidades. O acoplamento metálico é ideal para aplicações que exigem robustez e durabilidade, como em maquinários pesados e equipamentos industriais. Sua construção facilita a absorção de vibrações e choques, garantindo um funcionamento suave e prolongando a vida útil dos componentes.
Outra variação é o acoplamento elástico de pinos, que utiliza pinos de elasticidade para conectar as garras. Este tipo é conhecido por sua capacidade de amortecer vibrações e choques, tornando-o ideal para aplicações em que os eixos podem sofrer variações de carga. A flexibilidade do material elástico ajuda a reduzir o desgaste, o que pode ser uma vantagem significativa em ambientes de operação rigorosos.
Além disso, temos o acoplamento de garras de poliuretano. Este modelo oferece uma combinação de resistência e flexibilidade, sendo frequentemente usado em aplicações onde a absorção de choque é crucial. O poliuretano é um material leve, mas extremamente durável, que pode resistir a ambientes agressivos. Esse tipo de acoplamento é ideal para sistemas que requerem um bom desempenho em taxas de aceleração e desaceleração, como em equipamentos de transporte e sistemas de movimentação.
Os acoplamentos de garras de aço inoxidável também são uma opção popular, especialmente em indústrias onde a resistência à corrosão é fundamental, como na indústria farmacêutica e alimentícia. Esses acoplamentos são projetados para suportar ambientes Hostis, sendo resistentes a substâncias químicas e à umidade. O uso do aço inoxidável garante a integridade do acoplamento e a segurança dos processos industriais, evitando contaminação e falhas.
Uma variação interessante é o acoplamento de garras de perfil baixo. Esses modelos são projetados para aplicações onde o espaço é limitado, mas ainda é necessário manter uma conexão robusta. O design compacto permite que esses acoplamentos se encaixem em locais apertados, como em equipamentos eletrônicos e máquinas de pequeno porte, sem perder a eficácia da transmissão de torque.
Os acoplamentos de garras flutuantes também merecem destaque. Eles possuem a capacidade de se mover levemente, permitindo um melhor alinhamento entre os eixos mesmo em condições em que o desalinhamento pode ocorrer devido a variações térmicas ou vibrações. Esta característica é muito útil em sistemas móveis e dinâmicos, onde o controle de alinhamento é crítico para o funcionamento adequado das máquinas.
Existe ainda o acoplamento de garras de alta precisão, que é utilizado em aplicações que exigem um nível elevado de alinhamento e transmissão de torque. Este tipo de acoplamento consiste em garras projetadas para se encaixar perfeitamente, reduzindo ao máximo o jogo entre os eixos conectados. É comum em indústrias que utilizam máquinas CNC, onde a precisão é vital para a qualidade do produto final.
Ao escolher um tipo de acoplamento de garras, é importante considerar as especificidades de cada aplicação, como o tipo de carga, a velocidade, o alinhamento e as condições ambientais. A escolha do acoplamento adequado pode fazer uma diferença significativa no desempenho e na vida útil do equipamento.
Em resumo, os acoplamentos de garras são uma parte essencial de muitos sistemas industriais. Com uma variedade de tipos disponíveis, é possível encontrar o modelo ideal que atenderá às necessidades específicas de cada aplicação. Conhecer as características e benefícios de cada tipo de acoplamento de garras é fundamental para garantir eficiência e confiabilidade em projetos industriais.
Vantagens do Acoplamento de Garras
O acoplamento de garras é uma escolha popular em muitas indústrias devido às suas diversas vantagens. Sua estrutura simples e eficaz oferece benefícios significativos em relação a outros tipos de acoplamentos, tornando-o uma solução prática e confiável para a transmissão de torque entre eixos. Neste artigo, iremos explorar as principais vantagens do acoplamento de garras e o que o torna essencial em várias aplicações industriais.
Uma das maiores vantagens do acoplamento de garras é sua capacidade de acomodar desalinhamentos entre os eixos. Em sistemas onde os eixos não estão perfeitamente alinhados, o acoplamento de garras permite uma flexibilidade que ajuda a mitigar o desgaste e as falhas mecânicas. Essa flexibilidade é essencial em ambientes de operação onde as condições podem variar continuamente, como em fábricas e plantas de produção.
Além disso, os acoplamentos de garras são projetados para suportar altas cargas e torques. A robustez deste tipo de acoplamento permite que ele funcione de forma eficaz em aplicações que exigem grande força, como em sistemas de transporte e em maquinários pesados. Essa resistência ao mesmo tempo que proporciona segurança e eficiência nas operações.
Outra vantagem significativa é a facilidade de instalação e manutenção. O acoplamento de garras pode ser instalado rapidamente sem a necessidade de ferramentas especializadas, economizando tempo e esforço durante a montagem. Em termos de manutenção, como a estrutura é bastante simples, identificar potenciais problemas e realizar manutenções regulares torna-se uma tarefa mais fácil. A Durabilidade do material também significa que as trocas de componentes não são tão frequentes, o que contribui para a redução de custos operacionais.
A capacidade de suportar vibrações e choques é outra vantagem importante. O acoplamento de garras ajuda a suavizar as forças que afetam os componentes conectados, o que é um benefício significativo em operações onde as máquinas sofrem impactos frequentes. Esta propriedade é especialmente relevante em indústrias como a de mineração ou construção, onde as condições operacionais podem ser bastante severas.
O acoplamento de garras também é altamente versátil. Eles estão disponíveis em vários tamanhos e modelos, o que permite que sejam utilizados em diversas aplicações, desde pequenos motores elétricos até grandes sistemas de transmissão de energia. Essa versatilidade facilita a escolha do tipo certo para cada projeto, seja para um Acoplamento De Pino, acoplamento elástico, ou mesmo um acoplamento de precisão. Com tantas opções, fica mais fácil encontrar a solução ideal para as necessidades específicas de cada aplicação.
A resistência à corrosão é uma característica que vale a pena mencionar, especialmente quando se trata de acoplamentos de garras de aço inoxidável. Este material é ideal para ambientes onde a umidade e produtos químicos estão presentes, como em instalações de alimentos e bebidas, farmacêuticas e até mesmo na indústria química. A resistência à corrosão ajuda a garantir que o acoplamento mantenha sua integridade ao longo do tempo, evitando falhas que poderiam interromper as operações.
Outra vantagem do acoplamento de garras é a sua eficiência na transmissão de energia. Comparado a outros tipos de acoplamentos, os acoplamentos de garras minimizam as perdas de energia durante a transmissão de torque. Isso significa que a energia gerada por um motor pode ser transferida para a carga de maneira eficaz, resultando em melhor desempenho geral do sistema.
O design do acoplamento de garras também favorece a segurança. Como ele é projetado para durar e suportar tensões elevadas, a probabilidade de falhas é reduzida, o que aumenta a segurança no ambiente de trabalho. Além disso, o seu design minimiza os riscos de acidentes, uma vez que eles têm menos partes móveis que poderiam falhar ou se soltar durante a operação.
Por último, mas não menos importante, a ampla disponibilidade e o custo relativamente acessível dos acoplamentos de garras tornam-nos uma opção viável para muitas empresas. A popularidade desse tipo de acoplamento significa que existem muitos fornecedores e modelos disponíveis no mercado, permitindo que os compradores encontrem soluções de alta qualidade a preços competitivos.
Em conclusão, as vantagens do acoplamento de garras são muitas e variadas, tornando-o uma escolha valiosa para uma ampla gama de aplicações industriais. Sua capacidade de acomodar desalinhamentos, suportar altas cargas, facilidade de instalação, resistência à corrosão, eficiência na transmissão de energia e custo acessível são apenas algumas das razões pelas quais este tipo de acoplamento é tão amplamente utilizado. Compreender essas vantagens pode ajudar engenheiros e técnicos a tomar decisões informadas ao projetar ou atualizar sistemas de transmissão de torque em fábricas e indústrias.
Aplicações Comuns do Acoplamento de Garras
Os acoplamentos de garras são dispositivos amplamente utilizados em diversas indústrias devido à sua versatilidade e eficiência. Eles são projetados para conectar dois eixos rotativos, permitindo a transmissão de torque e movimento de maneira eficaz. Neste artigo, discutiremos as aplicações comuns do acoplamento de garras, destacando como este componente desempenha um papel vital em diferentes setores industriais.
Uma das aplicações mais frequentes dos acoplamentos de garras é em sistemas de transmissão de energia em máquinas industriais. Devido à sua capacidade de suportar altas cargas e acomodar desalinhamentos, eles são frequentemente utilizados em bombas, compressores e motores elétricos. Esses equipamentos, essenciais em processos de manufatura, dependem de uma conexão estável e confiável entre os eixos para operar com eficiência.
Além disso, acoplamentos de garras são frequentemente usados em máquinas de processamento material. Equipamentos como misturadores, transportadores e trituradoras se beneficiam dessas conexões, pois elas permitem a transmissão de torque necessário para mover materiais de maneira eficiente. Por exemplo, em uma linha de produção de alimentos, um acoplamento de garras pode ser utilizado para acionar transportadores que movem ingredientes entre diferentes etapas do processamento, garantindo que o fluxo de produção não seja interrompido.
Os acoplamentos de garras também desempenham um papel fundamental em aplicações de automação industrial. Em sistemas robóticos e em equipamentos de manuseio automático, a confiabilidade e a precisão da transmissão de movimento são cruciais. O uso de acoplamentos de garras permite um melhor alinhamento entre os motores e as partes móveis do robô, contribuindo para um movimento suave e controlado. Essa aplicação é especialmente importante em indústrias como a aeronáutica, automotiva e eletrônica, onde precisão e eficiência são exigidas.
Outra aplicação comum é no setor de energia. Os acoplamentos de garras são utilizados em geradores, turbinas eólicas e sistemas de geração de energia a gás. Em um gerador, por exemplo, o acoplamento liga o motor ao gerador, garantindo o torque necessário para a produção de eletricidade. Com a capacidade de absorver choques e minimizar vibrações, as garras proporcionam uma operação mais estável e eficiente, reduzindo a possibilidade de falhas mecânicas.
Na indústria ferroviária, os acoplamentos de garras são utilizados para conectar motores a sistemas de tração. A transmissão eficiente de potência é essencial para o funcionamento de trens e outros veículos ferroviários, e os acoplamentos de garras garantem que essa potência seja transmitida de forma confiável. Além disso, sua capacidade de suportar vibrações e condições adversas faz deles uma escolha popular em aplicações que exigem alta resistência.
O Acoplamento omega é um exemplo de acoplamento que oferece versatilidade em sua aplicação. Ele é utilizado em diversos setores, como automação, transporte e maquinário pesado. Essencialmente, qualquer setor industrial que exija uma conexão confiável entre eixos pode se beneficiar do uso de acoplamentos de garras, dada sua eficiência e robustez.
Outro setor que utiliza amplamente acoplamentos de garras é a construção civil. Equipamentos de construção, como escavadeiras e guindastes, dependem de uma transmissão de potência eficiente entre os motores e as partes móveis. A capacidade dos acoplamentos de garras de suportar desalinhamentos e choques os torna ideais para máquinas utilizadas em terrenos difíceis e em condições adversas.
A indústria do petróleo e gás também faz uso dos acoplamentos de garras. Em plataformas de perfuração, onde a transferência de torque é crítica para o sucesso das operações, esses acoplamentos garantem que a potência gerada pelos motores seja transmitida para os sistemas de perfuração de forma eficaz. A robustez e a confiabilidade dos acoplamentos de garras ajudam a garantir a segurança e o desempenho das operações em ambientes desafiadores.
Finalmente, os acoplamentos de garras são frequentemente utilizados em aplicações de transmissão de movimento em veículos. Eles são usados para conectar o motor ao sistema de transmissão, garantindo que a potência do motor seja transferida de maneira eficaz para as rodas. Essa aplicação é crucial para o desempenho e a eficiência dos veículos, destacando a importância dos acoplamentos de garras em uma variedade de contextos.
Em resumo, as aplicações comuns do acoplamento de garras são diversas e abrangem uma ampla gama de indústrias. Sua capacidade de suportar altas cargas, absorber vibrações e acomodar desalinhamentos os torna uma solução ideal para a transmissão de torque e movimento em várias máquinas e equipamentos. Com sua robustez e versatilidade, os acoplamentos de garras continuarão a desempenhar um papel fundamental na otimização de processos industriais e na melhoria da eficiência operacional.
Como Escolher o Acoplamento de Garras Ideal
Escolher o acoplamento de garras ideal é uma tarefa crucial para garantir a eficiência e a confiabilidade de sistemas mecânicos em diversas aplicações industriais. Existem inúmeras opções disponíveis no mercado, e a seleção correta depende de uma série de fatores técnicos e operacionais. Neste artigo, discutiremos os principais critérios a serem considerados ao escolher o acoplamento de garras mais adequado para suas necessidades específicas.
Um dos primeiros aspectos a serem avaliados é a carga e o torque que o acoplamento precisará suportar. É fundamental identificar o torque máximo que será transmitido entre os eixos. Se a aplicação exige alta potência, será necessário um acoplamento de garras projetado para lidar com essas cargas. A instalação inadequada ou a escolha de um acoplamento com capacidade de carga insuficiente pode resultar em falhas mecânicas e até em danos aos equipamentos.
Além da carga, o alinhamento dos eixos é um fator crucial na escolha do acoplamento de garras. É necessário considerar se os eixos estão corretamente alinhados e se haverá variações no alinhamento durante as operações. Os acoplamentos de garras têm a vantagem de acomodações menores de desalinhamento, mas a escolha do tipo certo dependerá da magnitude do desalinhamento esperado. Em situações em que o desalinhamento é significativo, um padrão de garras flexíveis pode ser mais apropriado.
Outro fator importante é a velocidade de operação. A velocidade à qual os eixos irão operar afetará a escolha do material e do design do acoplamento. Por exemplo, em aplicações de alta velocidade, como em motores elétricos industriais, é essencial escolher um acoplamento projetado para minimizar a vibração e o desgaste. Além disso, é preciso garantir que o material do acoplamento possa suportar as condições operacionais sem comprometer seu desempenho.
Os ambientes de operação também desempenham um papel fundamental na decisão. A presença de umidade, poeira, produtos químicos ou temperaturas extremas pode impactar a vida útil e o desempenho do acoplamento. Acoplamentos de garras fabricados em materiais como aço inoxidável ou plásticos de engenharia são opções ideais para ambientes agressivos, ajudando a garantir que o acoplamento permaneça funcional mesmo em condições desafiadoras.
Outra consideração relevante diz respeito ao espaço disponível para instalar o acoplamento. Em muitas aplicações, especialmente em espaços confinados, o tamanho do acoplamento pode ser um fator determinante. As garras podem ter diferentes dimensões, e um acoplamento de garras de perfil baixo pode ser mais adequado para esses cenários. A compatibilidade com outros componentes do sistema também deve ser considerada ao selecionar o tamanho do acoplamento.
Além dos critérios técnicos, o custo e a disponibilidade do acoplamento também são aspectos a serem considerados. É essencial comparar preços e opções no mercado, mas a escolha do acoplamento não deve ser baseada apenas no custo. A qualidade e a confiabilidade do acoplamento desempenham um papel significativo no impacto geral nos custos operacionais e de manutenção do sistema ao longo do tempo. Em aplicações críticas, pode ser mais vantajoso optar por um acoplamento de garras de maior qualidade, mesmo que o investimento inicial seja mais alto.
A durabilidade do acoplamento é um aspecto que complementa a análise de custo. Procure informações sobre a expectativa de vida e a resistência ao desgaste dos diferentes modelos disponíveis. Um acoplamento que apresenta maior durabilidade pode significar menos interrupções e custos de manutenção ao longo do tempo, equilibrando o custo inicial com o valor a longo prazo.
Outro ponto a ser considerado é a facilidade de instalação e manutenção do acoplamento. A complexidade do processo de instalação pode variar significativamente entre diferentes tipos de acoplamentos de garras. Um acoplamento que permite a instalação simples e rápida, bem como acesso fácil para manutenção e substituição, vai economizar tempo e reduzir custos operacionais.
Por fim, recomenda-se consultar fornecedores e especialistas na área. Profissionais com experiência em sistemas de transmissão de torque podem fornecer insights valiosos e ajudar na seleção do acoplamento de garras adequado com base em suas necessidades específicas. Além disso, é sempre vantajoso explorar as opções disponíveis no mercado, incluindo marcas e modelos que garantem a qualidade e a confiabilidade.
Em resumo, a escolha do acoplamento de garras ideal envolve uma análise cuidadosa de diferentes fatores, incluindo carga, alinhamento dos eixos, velocidade de operação, ambiente de trabalho, espaço disponível e custos. Optar por um acoplamento que se alinhe com suas necessidades específicas garantirá um sistema eficiente e confiável, minimizando problemas e aumentando a vida útil dos equipamentos. Com uma abordagem cuidadosa e informada, você poderá fazer uma escolha que traga benefícios a longo prazo para suas operações.
Instalação do Acoplamento de Garras
A instalação correta do acoplamento de garras é fundamental para garantir o desempenho eficaz e a durabilidade do sistema mecânico. Um acoplamento mal instalado pode causar falhas prematuras, desgaste excessivo e até danos aos componentes conectados. Neste artigo, abordaremos os passos essenciais para a instalação de acoplamentos de garras, discutindo as melhores práticas e questões a serem observadas durante o processo.
O primeiro passo na instalação do acoplamento de garras é a escolha do acoplamento apropriado, considerando as características da aplicação, como torque, velocidade, alinhamento e condições ambientais. Uma vez que o modelo certo é selecionado, é importante revisar as instruções do fabricante para se familiarizar com as especificidades do acoplamento escolhido.
Antes de iniciar a instalação, é necessário preparar os eixos que serão conectados. Eles devem estar limpos e livres de sujeira, graxa ou resíduos que possam comprometer a conexão. Utilizar um pano limpo ou compressor de ar pode ajudar a remover qualquer contaminação das superfícies dos eixos. A limpeza adequada é uma etapa crucial, pois sujeira ou resíduos podem afetar o alinhamento e a eficiência da transmissão de torque.
Uma vez que os eixos estão preparados, é importante verificar o alinhamento entre eles. O acoplamento de garras é projetado para acomodar pequenos desalinhamentos, mas desalinhamentos excessivos podem causar desgaste prematuro e falhas. Um alinhamento adequado reduz tensões indesejadas nos componentes, aumentando a vida útil do acoplamento e dos eixos conectados. Utilize ferramentas de alinhamento, como alinhadores de feixe ou régua de níveis, para garantir que os eixos estejam corretamente alinhados.
Após garantir o alinhamento, é hora de instalar o acoplamento de garras. Coloque cuidadosamente uma das garras no eixo de um lado e a outra garra no eixo oposto. O posicionamento deve ser feito com precisão, garantindo que as garras estejam alinhadas na posição correta. Alguns modelos de acoplamentos de garras possuem marcas ou direcionais que ajudam a indicar a melhor forma de instalação; sempre siga essas orientações.
É fundamental observar a correta colocação das garras, uma vez que a rotação dos eixos pode gerar forças consideráveis. Um erro comum durante a instalação é não aplicar o torque adequado nos parafusos de fixação. Verifique as especificações do fabricante quanto ao torque necessário para os parafusos, e utilize uma chave de torque para garantir que os parafusos estejam fixados de maneira uniforme e em conformidade com as recomendações.
Após a instalação inicial, é aconselhável realizar uma verificação visual para garantir que tudo esteja em ordem. Verifique se as garras estão bem posicionadas e se não há folgas entre o acoplamento e os eixos. Fique atento a quaisquer sinais de desalinhamento ou montagens incorretas que poderiam afetar o desempenho do sistema. Se necessário, ajuste a posição das garras para que elas fiquem corretamente alinhadas.
Uma vez que a instalação está concluída, é necessário executar testes para garantir que o acoplamento esteja funcionando adequadamente. Ligue o sistema e observe o funcionamento do acoplamento. Escute por ruídos incomuns, vibrações ou qualquer comportamento anormal. Se as garras estiverem bem instaladas, o sistema deverá operar suavemente e sem anomalias.
Outra etapa importante na instalação do acoplamento de garras é a manutenção regular. Assim como em qualquer sistema mecânico, os acoplamentos precisam ser verificados periodicamente para garantir seu funcionamento adequado. Durante essas verificações, preste atenção ao estado das garras, ao alinhamento e aos parafusos de fixação. Realizar manutenções proativas garantirá que o acoplamento mantenha sua eficácia ao longo do tempo. Em caso de desgastes visíveis, considere realizar a troca imediata do acoplamento para evitar falhas no sistema.
É aconselhável manter um registro das datas de instalação e das manutenções realizadas no acoplamento. Documentar essas informações pode facilitar a identificação de padrões de desgaste e ajudar a programar substituições quando necessário. Isso proporciona maior segurança em operações que dependem da confiabilidade do acoplamento de garras.
Por fim, em processos que exigem segurança, como a indústria de óleo e gás ou ambientes químicos, considere o uso de equipamentos de proteção individual (EPIs) durante a instalação. Ao trabalhar com ferramentas e componentes mecânicos, a segurança deve ser uma prioridade, garantindo que as normas e regulamentos sejam seguidos.
Em resumo, a instalação do acoplamento de garras é um processo que requer atenção aos detalhes, alinhamento correto e a utilização adequada das ferramentas. Seguir as diretrizes do fabricante, realizar manutenções periódicas e estar atento ao desempenho do sistema são práticas recomendadas que ajudarão a garantir a eficiência e a longevidade do acoplamento. Com um processo de instalação bem executado, você pode esperar um funcionamento eficaz e confiável do seu sistema de transmissão de torque.
Manutenção e Cuidados Necessários
A manutenção adequada e os cuidados necessários para acoplamentos de garras são essenciais para garantir seu desempenho ideal e prolongar a vida útil do sistema mecânico como um todo. Devido ao intenso uso em aplicações industriais, esses componentes estão sujeitos a desgastes e tensões que podem afetar sua eficiência ao longo do tempo. Neste artigo, vamos discutir as práticas de manutenção mais importantes e cuidados essenciais para garantir que seu acoplamento de garras funcione sempre a pleno vapor.
O primeiro passo na manutenção do acoplamento de garras é a realização de inspeções regulares. Esses exames devem ser programados em intervalos adequados, dependendo da intensidade do uso e das condições operacionais do equipamento. Durante as inspeções, é importante verificar visualmente o acoplamento quanto a qualquer sinal de desgaste, danos ou corrosão. Se houver sinais visíveis de deterioração, o componente deverá ser substituído imediatamente para evitar falhas mais graves no sistema.
A lubrificação adequada é também um aspecto crucial da manutenção do acoplamento de garras. Dependendo do tipo de acoplamento utilizado, pode ser necessário aplicar lubrificante nas garras para garantir um funcionamento suave. É importante seguir as recomendações do fabricante quanto ao tipo e à frequência de lubrificação. A falta de lubrificante pode resultar em atrito excessivo entre as partes móveis, levando ao desgaste prematuro e até mesmo à falha do acoplamento.
Além da lubrificação, o alinhamento dos eixos deve ser verificado periodicamente. Embora os acoplamentos de garras sejam projetados para tolerar pequenos desalinhamentos, um desalinhamento excessivo pode causar tensões adicionais e aumentar o desgaste. Ao realizar a manutenção, utilize ferramentas de alinhamento para garantir que os eixos permaneçam alinhados corretamente. Se necessário, ajuste a posição do acoplamento para corrigir qualquer desalinhamento que possa ter ocorrido durante a operação.
Outro cuidado importante diz respeito à fixação dos parafusos do acoplamento. Os parafusos devem ser inspecionados regularmente para garantir que estejam apertados adequadamente. O procedimento de aperto deve ser realizado de acordo com as especificações recomendadas pelo fabricante. Para evitar folgas ou vibrações excessivas, aperte os parafusos de forma uniforme, utilizando uma chave de torque para garantir que a pressão esteja dentro dos limites seguros. Na falta de uma verificação regular, os parafusos podem se soltar com o tempo, o que pode comprometer o funcionamento do sistema.
Deve-se estar atento ao ambiente operacional do acoplamento de garras. Se o acoplamento estiver exposto a condições adversas, como um ambiente úmido, químico ou com alta temperatura, é importante considerar o uso de materiais adequados que resistam a essas condições. Os acoplamentos fabricados em aço inoxidável ou materiais com resistência à corrosão são opções ideais para aplicações onde a exposição a produtos químicos ou à umidade é um problema. Inspecionar frequentemente as condições ambientais ao redor do acoplamento é uma prática recomendada que pode ajudar a prevenir danos antecipados.
Outra prática de manutenção importante é o monitoramento de vibrações. O uso de medidores de vibração durante a operação pode ajudar a detectar problemas potenciais antes que eles se tornem sérios. Vibrações excessivas podem indicar desalinhamento, desgaste ou falha em outras partes do sistema. Um monitoramento regular e a resposta rápida a qualquer alteração nas vibrações podem ajudar a evitar danos mais extensos e dispendiosos.
Além disso, considere a utilização de componentes adicionais para aumentar a vida útil do acoplamento. Filtros e isoladores de vibração podem ser instalados para melhorar o desempenho e reduzir os impactos sobre o acoplamento. Esses elementos ajudam a minimizar fatores externos que podem contribuir para o desgaste e a falha do sistema.
É recomendável também que todos os técnicos e operadores envolvidos no manuseio e manutenção dos acoplamentos de garras recebam treinamentos adequados. Eles devem estar cientes das melhores práticas de instalação, operação e manutenção, visando aumentar a conscientização sobre a importância de seguir as diretrizes e perceber o desempenho do acoplamento durante as operações. Isso não apenas melhora a vida útil do componente, mas também contribui para um ambiente de trabalho mais seguro.
Quando se trata de substituir um acoplamento de garras, escolha sempre produtos de qualidade de fornecedores confiáveis. Uma substituição inadequada pode impactar diretamente na eficiência mecânica do sistema. Considere opções que atendam às suas necessidades específicas e verifique se as especificações do novo acoplamento são compatíveis com os requisitos do sistema existente.
Por fim, mantenha um registro detalhado de todas as manutenções realizadas, bem como das condições operacionais e dos intervalos de inspeção. Esses registros são fundamentais para identificar padrões de desgaste e facilitar a programação de manutenções futuras. Com uma documentação adequada, é possível prever melhor as necessidades do sistema e implementar ações proativas em vez de reativas.
Em resumo, a manutenção e os cuidados necessários para os acoplamentos de garras são fundamentais para garantir uma operação eficiente e confiável. A implementação de práticas de inspeção regulares, lubrificação adequada, ajuste de alinhamento e monitoramento de vibrações ajudará a prolongar a vida útil do acoplamento. Investir em manutenção preventiva não apenas economiza custos com reparos, mas também aumenta a segurança e a eficiência operacional das instalações industriais.
Erro Comum ao Utilizar Acoplamento de Garras
O uso de acoplamentos de garras em aplicações industriais é amplamente aceito devido à sua eficiência e versatilidade. No entanto, há alguns erros comuns que podem ocorrer durante a seleção, instalação e operação desses componentes, comprometendo seu desempenho e a confiabilidade do sistema como um todo. Neste artigo, abordaremos os erros mais frequentes associados ao uso de acoplamentos de garras e como evitá-los.
Um dos erros mais comuns é a seleção inadequada do tipo de acoplamento de garras. É fundamental escolher um acoplamento que atenda às especificações da aplicação, considerando fatores como torque, velocidade e alinhamento dos eixos. Optar por um acoplamento que não suporta as cargas calculadas pode levar a falhas prematuras. Por outro lado, escolher um acoplamento excessivamente robusto pode resultar em custos desnecessários. Para evitar esse erro, é recomendável consultar as especificações do fabricante e, se necessário, buscar a orientação de um especialista para garantir que as necessidades específicas sejam atendidas.
Outro erro frequente está relacionado ao alinhamento dos eixos durante a instalação. Os acoplamentos de garras têm a capacidade de suportar pequenos desalinhamentos, mas o desalinhamento excessivo pode causar desgaste prematuro e falhas no sistema. Ignorar este aspecto pode resultar em vibrações indesejadas e tensões adversas nos componentes conectados. Portanto, é essencial utilizar ferramentas de alinhamento adequadas e garantir que os eixos estejam corretamente alinhados antes de fixar o acoplamento. Uma abordagem cuidadosa neste estágio pode evitar problemas significativos no futuro.
A fixação inadequada dos parafusos de instalação também é um erro comum a ser evitado. Os parafusos do acoplamento devem ser apertados até o torque recomendado pelo fabricante. O aperto excessivo pode causar danos ao acoplamento ou aos eixos, enquanto o aperto insuficiente pode resultar em folgas, levando a vibrações e desgaste prematuro. Para evitar esse erro, sempre siga as especificações de torque e verifique se os parafusos estão fixos durante as manutenções regulares.
O uso de acoplamentos de garras em ambientes inadequados é uma prática que pode resultar em falhas. Acoplamentos de garras expostos a umidade, produtos químicos corrosivos ou altas temperaturas podem deteriorar-se prematuramente, comprometendo o sistema. Portanto, ao selecionar um acoplamento, é importante considerar as condições ambientais da aplicação. Optar por acoplamentos feitos de materiais adequados, como aço inoxidável para ambientes corrosivos, é uma maneira eficaz de evitar danos.
Outro erro comum está relacionado à falta de manutenção e inspeção regular. Os acoplamentos de garras devem ser inspecionados periodicamente para garantir seu bom funcionamento. Ignorar essa prática pode levar ao acúmulo de desgaste e ao surgimento de problemas que podem ser detectados e solucionados precocemente. Verifique regularmente as condições do acoplamento, o alinhamento e a lubrificação, e tome as medidas corretivas necessárias. Essa abordagem preventiva ajudará a aumentar a vida útil do acoplamento e a confiabilidade do sistema.
A lubrificação inadequada é outro equívoco frequentemente cometido durante a operação de acoplamentos de garras. Alguns tipos de acoplamentos necessitam de lubrificação para garantir um funcionamento suave, enquanto outros são projetados para operar sem necessidade de lubrificação. É essencial seguir as recomendações do fabricante e usar o lubrificante apropriado. A falta de lubrificação pode causar atrito excessivo, levando a desgaste prematuro e falhas no componente. Por outro lado, a lubrificação excessiva deve ser evitada, uma vez que pode atrair sujeira e contaminantes, resultando em problemas semelhantes.
Os operadores também podem cometer erros ao tentar substituir um acoplamento de garras sem a devida atenção às especificações do novo componente. A escolha de um acoplamento que não atende aos requisitos de torque ou alinhamento, por exemplo, compromete o desempenho do sistema. É recomendável sempre utilizar unidades de substituição que sejam compatíveis com as especificações do modelo original, garantindo assim que o novo acoplamento atenda às necessidades do sistema.
Além disso, os operadores devem ser cuidadosos ao instalar um acoplamento de garras, certificando-se de que o direcionamento e a continuidade das garras estejam corretos. Uma instalação inadequada pode resultar em jogabilidade e vibração indesejadas, afetando a eficiência do sistema. Consulte as orientações do fabricante para garantir que o acoplamento esteja instalado na posição correta.
Por último, mas não menos importante, o erro de ignorar as recomendações do fabricante em relação à manutenção, instalação e operação do acoplamento de garras não deve ser subestimado. Os fabricantes fornecem diretrizes específicas e detalhes que são cruciais para o desempenho do equipamento. Certifique-se de seguir essas orientações para evitar problemas que podem resultar em falhas e ineficiência no sistema.
Em resumo, os erros comuns ao utilizar acoplamentos de garras podem ser evitados através de uma correta seleção, instalação cuidadosa, manutenção frequente e atenção às recomendações do fabricante. Ao eliminar esses erros, é possível garantir um funcionamento eficaz e confiável do sistema de transmissão de torque, aumentando a eficiência e prolongando a vida útil dos componentes envolvidos. A conscientização e a prática de boas técnicas na utilização de acoplamentos de garras não só ajudam a prevenir falhas, mas também promovem um ambiente de trabalho mais seguro e eficiente.
Em suma, o acoplamento de garras é um componente fundamental que desempenha um papel crucial na transmissão de torque em uma ampla variedade de aplicações industriais. A compreensão de suas características, tipos, vantagens e cuidados necessários é essencial para garantir um desempenho eficaz e prolongar a vida útil dos sistemas mecânicos. Ao seguir as orientações sobre como escolher, instalar e manter adequadamente os acoplamentos de garras, você poderá maximizar sua eficiência e minimizar o risco de falhas. Este conhecimento não só otimiza as operações industriais, mas também contribui para um ambiente de trabalho mais seguro e produtivo. Invista tempo em entender e aplicar esses conceitos, e sua operação industrial certamente verá melhorias significativas.