Acoplamento de Garras: Como Escolher o Ideal para Sua Aplicação
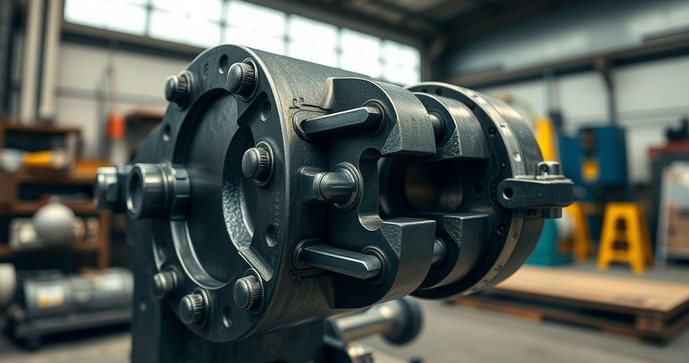
Por: Rodrigo - 20 de Março de 2025
O acoplamento de garras é um componente fundamental em sistemas mecânicos, proporcionando a conexão entre eixos e garantindo a transmissão eficiente de torque. Com diversas aplicações em indústrias, sua escolha correta pode impactar diretamente na performance e durabilidade dos equipamentos. Neste artigo, abordaremos os diferentes tipos de acoplamentos de garras, suas vantagens, dicas para seleção e cuidados necessários para manutenção.
Tipos de Acoplamento de Garras e Suas Aplicações
O acoplamento de garras é um dispositivo mecânico utilizado para conectar dois eixos, permitindo a transmissão de torque e movimento entre eles. Existem diferentes tipos de acoplamentos de garras, cada um com características específicas que os tornam mais adequados para determinadas aplicações. A seguir, exploraremos os principais tipos de acoplamento de garras e suas respectivas utilizações.
Um dos tipos mais comuns é o acoplamento de garras rígido. Este modelo é projetado para transmitir torque de forma eficiente, sem permitir qualquer movimento angular ou axial entre os eixos conectados. É ideal para aplicações onde a precisão é crucial, como em máquinas-ferramenta e equipamentos de medição. No entanto, sua rigidez pode ser uma desvantagem em situações onde vibrações ou desalinhamentos são comuns, pois não absorve choques ou desajustes.
Outro tipo amplamente utilizado é o acoplamento de garras flexível. Este modelo é projetado para acomodar desalinhamentos angulares e axiais, proporcionando uma maior flexibilidade em comparação ao acoplamento rígido. Os acoplamentos flexíveis são frequentemente utilizados em sistemas de transmissão de potência, como motores elétricos e redutores, onde pequenas variações de alinhamento podem ocorrer. Além disso, eles ajudam a reduzir o desgaste dos componentes, aumentando a vida útil do sistema.
O acoplamento de garras elástico é uma variação do acoplamento flexível, que utiliza um elemento elástico para absorver choques e vibrações. Este tipo de acoplamento é ideal para aplicações que envolvem cargas variáveis ou impactos, como em compressores e bombas. A capacidade de absorver choques ajuda a proteger os componentes do sistema, reduzindo o risco de falhas e prolongando a durabilidade do equipamento.
Uma opção interessante é o acoplamento tipo pneu, que se destaca pela sua capacidade de absorver vibrações e choques. Este modelo é composto por um corpo de borracha que se encaixa nas garras dos eixos, proporcionando uma conexão flexível e eficiente. O acoplamento tipo pneu é amplamente utilizado em aplicações que exigem um alto nível de amortecimento, como em sistemas de transporte e equipamentos industriais. Sua construção permite que ele suporte desalinhamentos e variações de carga, tornando-o uma escolha popular em ambientes industriais.
Além dos tipos mencionados, existem também os acoplamentos de garras de alta performance, que são projetados para aplicações específicas que exigem alta resistência e durabilidade. Esses acoplamentos são frequentemente utilizados em indústrias de alta tecnologia, como a aeroespacial e a automotiva, onde a precisão e a confiabilidade são essenciais. Eles podem ser fabricados com materiais avançados, como ligas metálicas e compósitos, para atender às exigências rigorosas dessas aplicações.
Outro tipo importante é o acoplamento de garras de segurança, que é projetado para proteger o sistema contra sobrecargas e falhas. Este modelo é equipado com dispositivos de segurança que permitem a desconexão automática dos eixos em caso de falha, evitando danos ao equipamento e garantindo a segurança do operador. Os acoplamentos de segurança são frequentemente utilizados em aplicações industriais pesadas, onde o risco de falhas é maior.
Em resumo, a escolha do tipo de acoplamento de garras adequado depende das necessidades específicas da aplicação. Fatores como alinhamento, flexibilidade, capacidade de absorção de choques e requisitos de segurança devem ser considerados ao selecionar o acoplamento ideal. Compreender as características e aplicações de cada tipo de acoplamento de garras pode ajudar engenheiros e profissionais a tomar decisões informadas, garantindo a eficiência e a durabilidade dos sistemas mecânicos.
Independentemente do tipo escolhido, é fundamental realizar a manutenção adequada dos acoplamentos de garras para garantir seu funcionamento eficiente. Inspeções regulares e substituições quando necessário podem prevenir falhas e prolongar a vida útil do equipamento, contribuindo para a eficiência operacional e a segurança do ambiente de trabalho.
Vantagens do Acoplamento de Garras em Sistemas Mecânicos
O acoplamento de garras é um componente essencial em sistemas mecânicos, oferecendo uma série de vantagens que o tornam uma escolha popular em diversas aplicações industriais. Sua capacidade de conectar eixos de forma eficiente e confiável é fundamental para o desempenho de máquinas e equipamentos. Neste artigo, exploraremos as principais vantagens do acoplamento de garras e como ele pode beneficiar diferentes sistemas mecânicos.
Uma das principais vantagens do acoplamento de garras é a sua eficiência na transmissão de torque. Este tipo de acoplamento é projetado para minimizar as perdas de energia durante a transmissão, garantindo que a potência gerada pelo motor seja transferida de forma eficaz para o equipamento acionado. Isso é especialmente importante em aplicações industriais, onde a eficiência energética pode impactar significativamente os custos operacionais.
Além disso, os acoplamentos de garras são conhecidos por sua robustez e durabilidade. Fabricados com materiais de alta resistência, eles são capazes de suportar condições adversas, como altas temperaturas, umidade e exposição a produtos químicos. Essa resistência torna os acoplamentos de garras ideais para ambientes industriais exigentes, onde a confiabilidade é crucial para evitar paradas não programadas e custos de manutenção elevados.
Outra vantagem significativa é a capacidade de absorver vibrações e choques. Em sistemas mecânicos, vibrações e impactos podem causar desgaste prematuro dos componentes e falhas no equipamento. Os acoplamentos de garras, especialmente os modelos flexíveis, são projetados para acomodar desalinhamentos e absorver choques, protegendo assim os eixos e outros componentes do sistema. Isso não apenas aumenta a vida útil do equipamento, mas também melhora o desempenho geral do sistema.
Os acoplamentos de garras também oferecem facilidade de instalação e manutenção. A maioria dos modelos é projetada para ser instalada rapidamente, sem a necessidade de ferramentas especiais ou habilidades técnicas avançadas. Isso reduz o tempo de inatividade durante a instalação e facilita a substituição em caso de falhas. Além disso, a manutenção é geralmente simples, exigindo apenas inspeções regulares e lubrificação, o que contribui para a eficiência operacional.
Outro ponto a ser destacado é a versatilidade dos acoplamentos de garras. Eles podem ser utilizados em uma ampla gama de aplicações, desde pequenos motores elétricos até grandes sistemas industriais. Essa versatilidade permite que os engenheiros escolham o acoplamento mais adequado para suas necessidades específicas, garantindo que o sistema funcione de maneira otimizada. Além disso, existem diferentes tipos de acoplamentos de garras, como o acoplamento elástico de pinos, que oferecem características específicas para atender a diferentes requisitos de desempenho.
A redução de ruído é outra vantagem importante dos acoplamentos de garras, especialmente em aplicações onde o nível de ruído é uma preocupação. Os modelos flexíveis e elásticos ajudam a minimizar o som gerado durante a operação, proporcionando um ambiente de trabalho mais confortável e seguro. Isso é particularmente relevante em indústrias onde a conformidade com normas de segurança e saúde ocupacional é necessária.
Além disso, os acoplamentos de garras são projetados para oferecer alta precisão de alinhamento. Um alinhamento adequado é crucial para o funcionamento eficiente de qualquer sistema mecânico, e os acoplamentos de garras ajudam a garantir que os eixos permaneçam alinhados durante a operação. Isso reduz o desgaste e prolonga a vida útil dos componentes, contribuindo para a eficiência geral do sistema.
Por fim, a custo-benefício dos acoplamentos de garras é uma vantagem que não pode ser ignorada. Embora o investimento inicial possa variar dependendo do tipo e da aplicação, a durabilidade e a eficiência desses acoplamentos geralmente resultam em economias significativas a longo prazo. A redução de custos com manutenção e a minimização de paradas não programadas contribuem para um retorno sobre o investimento mais rápido e eficaz.
Em resumo, as vantagens do acoplamento de garras em sistemas mecânicos são numerosas e significativas. Desde a eficiência na transmissão de torque até a robustez e durabilidade, esses componentes desempenham um papel crucial no desempenho e na confiabilidade de máquinas e equipamentos. Ao considerar a implementação de acoplamentos de garras em sistemas mecânicos, é importante avaliar as necessidades específicas da aplicação e escolher o tipo mais adequado para garantir o máximo desempenho e eficiência.
Como Escolher o Acoplamento de Garras Ideal
A escolha do acoplamento de garras ideal é um passo crucial para garantir a eficiência e a durabilidade de sistemas mecânicos. Com uma variedade de opções disponíveis no mercado, é fundamental considerar diversos fatores antes de tomar uma decisão. Neste artigo, abordaremos os principais critérios a serem avaliados na seleção do acoplamento de garras mais adequado para suas necessidades.
Um dos primeiros aspectos a considerar é o tipo de aplicação. O ambiente em que o acoplamento será utilizado pode influenciar diretamente na escolha do modelo. Por exemplo, se o acoplamento será exposto a altas temperaturas, umidade ou produtos químicos, é essencial optar por materiais que resistam a essas condições. Acoplamentos de garras fabricados com materiais de alta resistência, como aço inoxidável ou ligas especiais, são recomendados para aplicações em ambientes agressivos.
Outro fator importante é a potência e o torque que o sistema irá demandar. Cada acoplamento de garras possui uma capacidade de torque específica, e é fundamental escolher um modelo que suporte a carga máxima esperada. Para isso, é necessário calcular o torque que será transmitido pelo motor e garantir que o acoplamento escolhido tenha uma margem de segurança adequada. Ignorar esse aspecto pode resultar em falhas prematuras e danos ao equipamento.
Além disso, a flexibilidade e o alinhamento são características que devem ser avaliadas. Em sistemas onde o desalinhamento é uma possibilidade, como em motores e redutores, um acoplamento de garras flexível pode ser a melhor opção. Esses modelos são projetados para acomodar desalinhamentos angulares e axiais, reduzindo o desgaste dos componentes e aumentando a vida útil do sistema. Por outro lado, se o alinhamento for preciso e constante, um acoplamento rígido pode ser mais adequado, proporcionando uma transmissão de torque mais eficiente.
A facilidade de instalação e manutenção também deve ser considerada. Alguns acoplamentos de garras são projetados para serem instalados rapidamente, sem a necessidade de ferramentas especiais. Isso pode ser um fator decisivo em ambientes industriais, onde o tempo de inatividade deve ser minimizado. Além disso, a manutenção regular é essencial para garantir o funcionamento eficiente do acoplamento. Escolher um modelo que exija menos manutenção pode ser uma vantagem significativa a longo prazo.
Outro aspecto a ser considerado é o custo. Embora o preço não deva ser o único critério de escolha, é importante avaliar o custo-benefício do acoplamento. Modelos mais baratos podem parecer atraentes, mas se não atenderem às necessidades específicas da aplicação, podem resultar em custos adicionais com manutenção e substituição. Portanto, é recomendável investir em um acoplamento de qualidade que ofereça durabilidade e eficiência, como o acoplamento omega, que é conhecido por sua confiabilidade em diversas aplicações.
A redução de ruído também pode ser um critério importante, especialmente em ambientes onde o controle de som é necessário. Acoplamentos de garras que oferecem características de amortecimento podem ajudar a minimizar o ruído gerado durante a operação, proporcionando um ambiente de trabalho mais confortável. Isso é particularmente relevante em indústrias onde a conformidade com normas de segurança e saúde ocupacional é necessária.
Além disso, a compatibilidade com outros componentes do sistema deve ser avaliada. É fundamental garantir que o acoplamento escolhido seja compatível com os eixos e motores que serão utilizados. Isso inclui verificar o diâmetro dos eixos, o tipo de conexão e as especificações de torque. A falta de compatibilidade pode resultar em falhas no sistema e danos aos componentes.
Por fim, é recomendável consultar especialistas ou fornecedores ao escolher o acoplamento de garras ideal. Profissionais com experiência na área podem oferecer orientações valiosas e ajudar a identificar o modelo mais adequado para suas necessidades específicas. Além disso, muitos fornecedores oferecem suporte técnico e informações detalhadas sobre os produtos, o que pode facilitar a tomada de decisão.
Em resumo, a escolha do acoplamento de garras ideal envolve a consideração de diversos fatores, incluindo o tipo de aplicação, potência, flexibilidade, facilidade de instalação, custo e compatibilidade. Avaliar cuidadosamente essas características garantirá que você selecione um acoplamento que atenda às suas necessidades e contribua para a eficiência e durabilidade do seu sistema mecânico. Com a escolha certa, você poderá maximizar o desempenho do seu equipamento e minimizar os custos operacionais a longo prazo.
Manutenção e Cuidados com Acoplamentos de Garras
A manutenção adequada dos acoplamentos de garras é essencial para garantir o desempenho eficiente e a durabilidade dos sistemas mecânicos. Esses componentes desempenham um papel crucial na transmissão de torque e movimento entre eixos, e sua falha pode resultar em paradas não programadas e custos elevados de reparo. Neste artigo, abordaremos as melhores práticas de manutenção e cuidados que devem ser adotados para prolongar a vida útil dos acoplamentos de garras.
Um dos primeiros passos na manutenção de acoplamentos de garras é a inspeção regular. É recomendável realizar verificações periódicas para identificar sinais de desgaste, danos ou desalinhamento. Durante a inspeção, verifique se há folgas excessivas, rachaduras ou deformações nas garras e nos componentes do acoplamento. Qualquer sinal de dano deve ser tratado imediatamente, pois pode comprometer a eficiência do sistema e levar a falhas mais graves.
A limpeza é outro aspecto importante da manutenção. A sujeira e a poeira podem se acumular ao redor do acoplamento, interferindo em seu funcionamento. Utilize um pano seco ou uma escova macia para remover detritos e sujeira acumulada. Evite o uso de solventes agressivos que possam danificar os materiais do acoplamento. Manter a área ao redor do acoplamento limpa também ajuda a prevenir a entrada de contaminantes que podem causar desgaste prematuro.
Além da limpeza, a lubrificação adequada é fundamental para o funcionamento eficiente dos acoplamentos de garras. A lubrificação reduz o atrito entre as partes móveis, minimizando o desgaste e prolongando a vida útil do componente. Consulte as recomendações do fabricante para determinar o tipo de lubrificante adequado e a frequência de aplicação. Em geral, a lubrificação deve ser realizada a cada seis meses, mas isso pode variar dependendo das condições de operação e da frequência de uso.
Outro ponto a ser considerado é o alinhamento dos eixos. Um alinhamento inadequado pode causar desgaste excessivo e falhas no acoplamento. É importante garantir que os eixos estejam alinhados corretamente durante a instalação e ao longo do tempo. Utilize ferramentas de alinhamento apropriadas para verificar e ajustar o alinhamento conforme necessário. Um alinhamento preciso não apenas aumenta a eficiência do acoplamento, mas também reduz o risco de falhas em outros componentes do sistema.
Os acoplamentos de garras também podem ser afetados por vibrações excessivas. Vibrações podem ser causadas por desalinhamento, desequilíbrio ou problemas mecânicos em outros componentes do sistema. É importante monitorar as vibrações e, se necessário, realizar ajustes para minimizar seu impacto. O uso de acoplamentos que absorvem vibrações, como o acoplamento de fole, pode ser uma solução eficaz para reduzir os efeitos das vibrações e proteger os componentes do sistema.
Além disso, a substituição de acoplamentos de garras deve ser considerada quando os sinais de desgaste se tornam evidentes. Mesmo com manutenção regular, os acoplamentos têm uma vida útil limitada e eventualmente precisarão ser substituídos. É importante seguir as recomendações do fabricante quanto à vida útil do acoplamento e realizar a substituição antes que ocorra uma falha. A substituição oportuna pode evitar paradas inesperadas e custos elevados de reparo.
Outro aspecto importante da manutenção é a documentação. Manter registros detalhados das inspeções, limpezas, lubrificações e substituições realizadas pode ajudar a identificar padrões de desgaste e a planejar a manutenção futura. Essa documentação também pode ser útil para garantir a conformidade com as normas de segurança e qualidade, além de facilitar a comunicação com fornecedores e técnicos de manutenção.
Por fim, é recomendável treinar a equipe responsável pela manutenção dos acoplamentos de garras. O conhecimento adequado sobre as melhores práticas de manutenção e cuidados pode fazer uma diferença significativa na eficiência e na durabilidade dos componentes. Oferecer treinamentos regulares e atualizações sobre novas tecnologias e práticas de manutenção pode ajudar a garantir que a equipe esteja sempre preparada para lidar com os desafios que surgem.
Em resumo, a manutenção e os cuidados com acoplamentos de garras são fundamentais para garantir o desempenho eficiente e a durabilidade dos sistemas mecânicos. Inspeções regulares, limpeza, lubrificação, alinhamento e monitoramento de vibrações são práticas essenciais que devem ser adotadas. Além disso, a documentação e o treinamento da equipe são aspectos importantes que contribuem para a eficácia da manutenção. Ao seguir essas diretrizes, você pode maximizar a vida útil dos acoplamentos de garras e minimizar os custos operacionais associados a falhas e reparos.
Em conclusão, o acoplamento de garras desempenha um papel crucial na eficiência e confiabilidade de sistemas mecânicos. A escolha do tipo adequado, considerando fatores como aplicação, potência e alinhamento, é essencial para garantir um desempenho otimizado. Além disso, a manutenção regular e os cuidados apropriados são fundamentais para prolongar a vida útil desses componentes e evitar falhas dispendiosas. Ao seguir as diretrizes apresentadas, é possível maximizar a eficiência operacional e assegurar que os equipamentos funcionem de maneira eficaz, contribuindo para a produtividade e a segurança nas operações industriais.